【リコー社内実践事例】
3Dプリンターによる
『ものづくり改革』
プロジェクト
~Design for Additive Manufacturingを
自社製品で実践~
『ものづくり改革』
プロジェクト概要

3Dプリンター出力サービスチームと商用印刷機の設計者・生産技術者が討議し、本製品の部品を3Dプリンター造形品に置き換えて製品仕様が実現できるのか、そして3Dプリンターと新たな設計(Design for Additive Manufacturing*)の効果を測るプロジェクトに挑戦しました。
*Design for Additive Manufacturing:従来の設計方法にとらわれない、3Dプリンターでの造形を前提とした設計方法
“リコー出力サービス”では最先端の3Dプリンターを駆使し、お客様に、Design for Additive Manufacturingによる3Dプリンターの価値をご提供しています。近年、需要が増えているダイレクト部品の3Dプリンター造形に対し、メーカーリコーの設計現場を見ると、3Dプリンター活用用途はまだ試作に限られていました。そのような状況の中、自分たちの商品で3Dプリンターの実力を確かめるという活動に取り組み、その成果によって、リコー社内での3Dプリンターに対する評価は大きく変わりました。
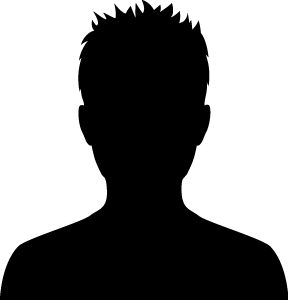
造形サービス事業室 室長
3DプリンターとDesign for Additive Manufacturingによるメリット

①一体化・材料代替・中抜きによる軽量化
②複数部品の一体化による部品数・組み立て工数削減
③3Dプリンター造形ならではの、品質・機能・意匠による付加価値を創出
プロジェクト担当者の声

実際に開発に携わった設計者・生産技術者に、部品ごとの機能・リモデリングでの部品への改良ポイントを聞いた上で、3Dプリンター向け設計(Design for Additive Manufacturing)を提供・実現できたので、3Dプリンターのポテンシャルが最大限発揮されたと思います。
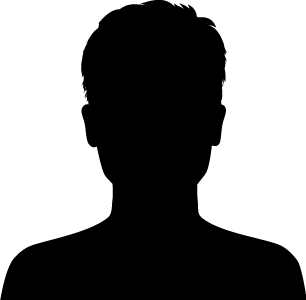
技術者
今までは自部署の小型FDMで造形していて、それが3Dプリンターの実力だと思っていましたが、大間違い。用途によって方式・材料を選択し、その方式に合わせた設計手法(Design for Additive Manufacturing)があることが分かりました。
これは使える !
これは使える !
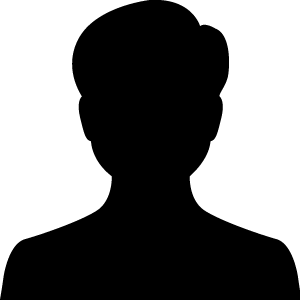
もし生産準備の段階でこれら3Dプリンターがあったら、仮型の改修作業や複雑形状のモールド金型製作時の試行錯誤が格段に減らせる可能性があったということが分かりました。一体化による組立レスは、今後の生産ラインづくりに非常に大きな効果を出せると感じました。
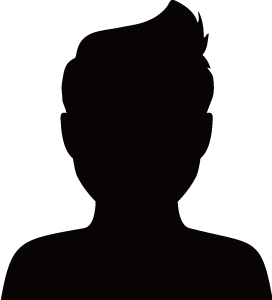