ハイブリッドドローンが生み出す新たな社会の実現
3Dプリンターが支える国産ドローン開発の現場
株式会社エアロジーラボ様は、大型の産業用ドローンを企画・設計・製造、そして販売まで手掛ける企業です。従来の通常のドローンの飛行時間は一般的に10~20分程度でしたが、エアロジーラボ様のドローンでは、ガソリンエンジンとバッテリーモーターの両方を使ったハイブリッドシステムの採用により長時間飛行を実現。従来では難しかった離島や過疎地への物流インフラとしての活用を始め、災害現場における捜索活動や救助活動への利用も期待されています。そこでエアロジーラボ様ではこれらのニーズに的確に応え、さらなる高品質・高性能なドローン製品の開発を加速させるため、造形精度が高く、最終製品としての使用にも耐え得る強度が実現できる3Dプリンターを導入し製作作業の効率化と製品の高品質化を実現。
ドローンの社会実装促進を目指し、日々チャレンジを続けています。
- 所在地:
- 大阪府箕面市
- 従業員数:
- 20名
- 主な業務:
- ◎UAV(無人飛行機)の開発、設計、製造、販売
- ◎各種実験・開発受託
- ◎空中撮影及び各種映像制作
- ホームページURL:
- https://aerog-lab.com/
従来の金型を使った部品製作の手間を、3Dプリンターが解決
高い造形精度で出力される部品は、サイズ調整することなく組み立てが可能
従来の金型で部品を製作する場合だと、抜き勾配や金型同士がちゃんと離型できるかなどを考える必要がありましたが、直接部品を造形できる3Dプリンターではそういった手間がいらず、設計時の自由度が大きく広がりました。また、従来の3Dプリンターの造形精度では、出力した部品をきちんと組み合わせるために、何度もサイズ調整しながら出力していましたが、「Mark Two」の高い造形精度により、部品のサイズ調整をすることなく組み立てが可能になり作業効率がアップしました。
生み出すには、形状構造の制約の中で自由な設計が必須。
導入した機器/サービス
Mark Two独自の材料で造形した部品は高い強度が出るということと、造形精度が高いというのが導入の決め手でした。
お客様インタビューCustomer Interview
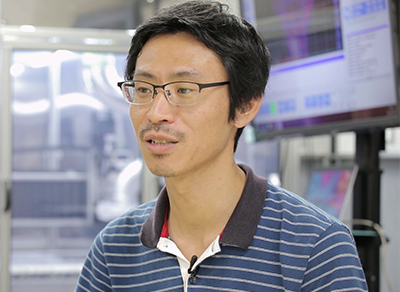
- 株式会社 エアロジーラボ
- 開発部マネージャー
前原明様
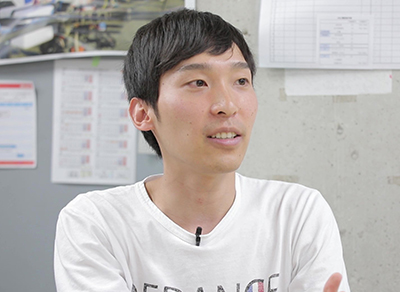
- 株式会社 エアロジーラボ
- 開発部
田嶋良太様
背景・課題
これまでは金型を使って部品を製作していたのですが、その場合、抜き勾配(金型から成形品をスムーズに抜くための傾斜)を考えなければらならなかったり、金型同士がちゃんと離型できるかなどを考慮する必要があり、そういった制約から設計時の制約が多く自由度が低いと感じていました。また、従来の3Dプリンターだと、部品同士を組み合わせる時の寸法公差(図面の寸法に対して許容される誤差の範囲)をある程度考慮しないと上手く組合せできないということがあり、何度も出力を繰り返してサイズを調整する作業が必要になり、開発効率が悪いという問題がありました。
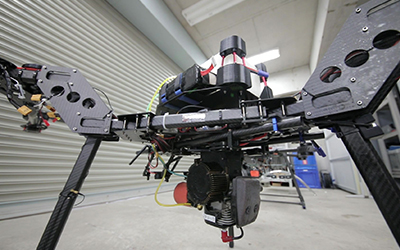
導入のポイント
ドローンは空を飛ぶものなので、その部品には第一に「軽さ」が求められると共に、「強度」が必要とされるのですが、Mark Twoはカーボンやナイロンにファイバー素材を織り込んだ独自の造形材料で「軽さと強度を両立した部品」を「自由設計」で製作できるというのが大きな決め手でした。今までの同様な造形方式(材料押出堆積法/FDM)の3Dプリンターで使っているPLAなどの造形材料のもとと比較すると明らかに強度があり、造形精度も高いと思いました。さらに展示会で造形された物を見たときに、そのまま製品としてリリースできるくらい表面の仕上がりが非常に綺麗で、是非使ってみたいなと感じました。既製品ではない現状のドローンの基本形状の構成としては、カーボンプレートとパイプを組み合わせたものが前提となりますが、その中で自由な設計ができないと取り付けができないものが多々あり、そういった意味でも3Dプリンターの導入は必然でした。
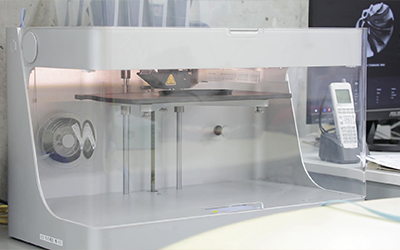
Markforged Mark Two
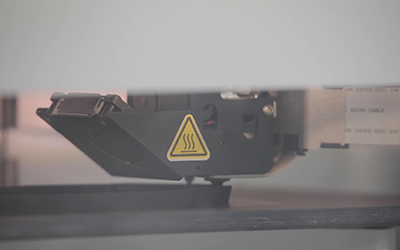
導入の効果
射出成形での部品製作ではあり得なかった柔軟な部品設計が可能に
Mark Two独自の材料で造形した部品にはストレッチ性(バネ性)があり、出力した部品を組み立てる際に、組み立て部分を広げて取り付けたりといったことができるようになりました。ポリカーボネートやABSを射出成形で部品を作る際には、当然、材料自体にストレッチ性(バネ性)があるという考えは一切なかったのですが、Mark Twoで部品を設計する際にはそういったストレッチ性も考慮した柔軟な発想で設計が可能になりました。
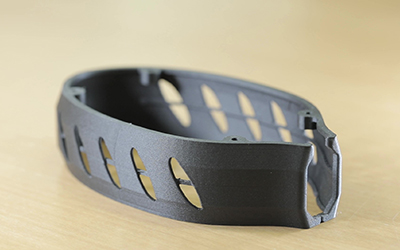
3Dプリンター製造の最終パーツ
設計通りのサイズで正確に造形される精度に驚き
従来の3Dプリンターの造形精度だと、出力した部品同士を組み合わせる際の寸法公差をある程度考慮しないと、上手く組めないということがあり、何度も部品を出力してサイズ調整を繰り返す作業が必要でした。Mark Twoの場合は入力した寸法でキッチリと造形されるので、最初はびっくりしました。 例えばパイプのサイズ径を入力して出力すれば、それにキッチリ合うものが出来上がって来ます。そのまま何の調整もなく組み合わせることができるので、作業効率が飛躍的にアップしました。
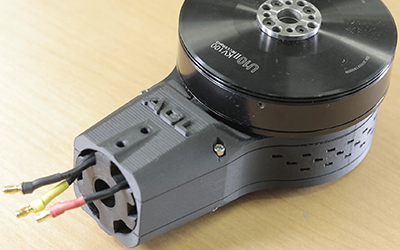
今後の展望
私たちが製作しているハイブリッドドローンの最大の特徴は「長時間飛行できる」ということです。 従来のバッテリー式ドローンの飛行時間はせいぜい10〜20分と、実際の物流に使用できるレベルではありませんでした。 そういったドローンの弱点を解決するのが、従来のバッテリーモーターとガソリンエンジンの両方を使ったハイブリッドシステムです。 現在私たちが製作しているハイブリッドドローンの飛行時間は2〜3時間で、これまでのドローンの世界とは別次元のレベルです。 離島や過疎地への物流インフラとして活用し買い物難民を救済する、災害現場で捜索や物資輸送などの活動をする、他にも危険が伴う巨大建造物の検査など、人命がかかわるような分野にもどんどんドローンを進出させていきたいと考えています。そうやってドローンを社会実装して世の中を変えたい。それが私たちエアロジーラボの本命と考えています。