3Dプリンターによる治具で生産プロセスを抜本的に改善。
組み立て品質が向上し、月間不具合件数がゼロに!
小ロット高付加価値の大型プリンターを製造するリコーインダストリー株式会社では、製品組立工程で一人の作業者が大量の類似パーツを扱うために、部品の取り間違えなどのミスが発生しやすく、組立ミス低減と生産効率化が大きな課題でした。 従来手法では改善が頭打ちになっていたが、3Dプリンターを活用した組立て治具製作と生産ラインの再構築により生産プロセス全体の見直しに成功。組立ミス撲滅と生産効率の向上を同時に達成しました。
- リコーグループの生産子会社として、複写機・複合機、キーパーツ、トナー等の生産・販売を行う
- 業種:機械メーカー / 従業員数:3078名(2016年4月)
組立用の治具づくりに3Dプリンターを活用し、生産プロセスを見直し
リコーインダストリーが生産している大型の商用プリンターは部品点数が多く、製造現場では組み立て作業の複雑化により作業ミスが発生しやすく、作業ミスの低減が課題でした。作業工程を改善するため、3Dプリンターで造形した治具を積極的に活用し、ミスの低減や生産性アップの効果を実現しています。
導入した機器/サービス
自社の生産プロセスにおいてどのように3Dプリンターを活用できるのか?
導入後の改善効果シミュレーションを含めたトータルなコンサルティングをリコーにお願いしました。
導入したプリンターでは作れない大型の治具や、精度が求めれるもの、造形後の後加工が必要な特殊な治具等については、リコーの出力サービスを使ってアウトソーシングしています。
プラスチック同等の材料であるABS樹脂が使えるプリンターを選択。簡易治具として利用できるくらいの強度があれば、審美性や耐熱/耐水などのスペックは必要ないため、エントリーモデルの3Dプリンターを導入しました。
背景・課題
複雑な作業における作業ミス低減が課題
リコーグループでは海外生産拠点の増加に伴い、国内生産は"小ロットの高機能・高付加価値商品"へシフトしており、現在国内で生産している製品の多くは大型の商用プリンターが中心です。ただ、これらの製品は高機能であるが故に部品点数も非常に多く、組み立て作業も複雑です。
作業を補助するための治具は利用していましたが、生産準備にかかるコストと時間が多大で、また、外注すると完成品が届くまでに3週間近くかかることもあるため、実際には追加工や設計変更があったとしても、やむを得ずそのまま使っているという状況が続いていました。「部品の多さ」、「作業の複雑さ」、「最適化されない治具」という状況の中、組立てミスを低減し、いかに作業品質を向上させるかが大きな課題でした。
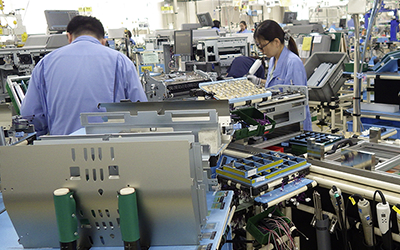
従来の発想では、改善の効果も頭打ちに
ミスの低減だけでなく、生産性の改善も大きなテーマとなっていました。大型機は作業者1人当り数百点もの部品を組立てる必要があり、いかに素早く部品を集めて効率的に組み上げるかがカギとなります。しかし、従来の作業台を中心とした工程設計がさらなる改善を実現するための足かせになってしました。
従来の生産ラインでは、組立ユニット単位で設けた作業台に金属製の治具を固定し、周囲に大量の部品を並べ、「作業台の周囲にいかに効率的に部品や工具を集めるか」を追求してきた結果、作業スペースが手狭になったうえ、作業者は複数の作業台を渡り歩きながら、数種類のサブパーツを組み上げなければなりませんでした。「作業台ありきの発想では改善も頭打ちで、これ以上の改善は難しいと感じていました」(平間氏)抜本的な解決策の必要性を感じていた折、3Dプリンターのことを知り、その可能性に惹かれました。
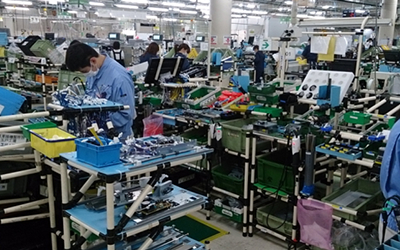
導入のポイント
コンサルティングで具体的な改善ポイントを洗い出し
3Dプリンターの可能性は感じつつも、今の生産工程にどう活用していくべきか具体的なイメージが固まらなかったため、リコーにコンサルティングをお願いすることにしました。
改善にあたって、まず着目したのが大型プリンター製造のプリンターユニットの組立工程とモーター部品の組立工程でした。リコーのコンサルタントが作業現場でヒアリングし、作業内容や作業動線の分析を重ねることで、作業品質や作業効率の面でいくつかの問題点が見えてきました。問題を分析した結果、「3Dプリンターの特徴を活かした治工具の作成で多くの工程改善が見込めること、また、それらの改善を進めることで生産ライン自体の改善が図れると考えました。」
リコーのコンサルタントと現場関係者で改善目標を共有し、プロジェクトを発足。現状の治工具や作業内容の詳細分析を進め、3Dプリンターによる新しい治工具の設計と作成に取り掛かりました。当初、治工具の設計と作成はリコーへ委託、「設計・製造を熟知した担当者が対応してくれるので、安心して任せられました。」
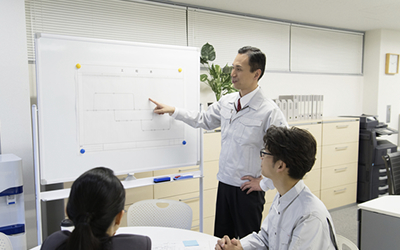
治具の用途に応じて、内製とアウトソーシングを使い分け
今回、3Dプリンターで製作した治工具は、形状が比較的簡易なものから複雑なものまで多岐にわたります。当然ハイエンドの3Dプリンターを導入すれば簡易なものから複雑なものまで造形することはできますが、費用対効果の面から現実的でなはいと考えました。そこで、プロジェクトでは「簡易治工具を作るのに最適な3Dプリンター」という観点から、FDM方式のデスクトップ機『Leapfrog Creatr HS』を現場に導入しました。エントリーモデルのため、素材やスペック(耐水/耐熱/審美性)に制約はありますが、簡易治工具を作成するには十分でした。また、より複雑な形状や高い精度が求められる治工具を製作する場合は、『3Dプリンター 出力サービス』を利用しました。
内製とアウトソーシングサービスをうまく使い分ける投資効果の高い提案をリコーがしてくれたので、プロジェクトをスムーズに進めることができ、現場の状況を良く理解してくれているという安心感にもつながりました。
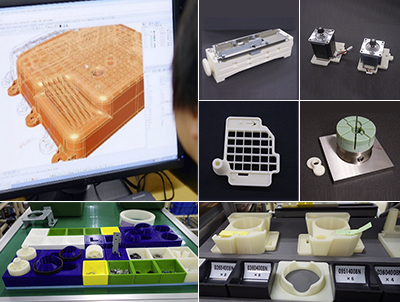
導入の効果
3Dプリンターの特徴を活かした柔軟なアイデアが従来の治工具の常識を変える
改善プロジェクトでは、3Dプリンターでの試作を繰り返しながら、様々な治工具を作成し、各工程への導入を進めました。
配膳治具・組立治具の改善で、『配膳・組立ミスが0件』、『作業習熟時間を50%短縮』
従来の切削加工等による治具の場合、形状を複雑にするほどコストアップになるため、コストを抑えるために治具の分かりやすさや使いやすさが犠牲になっていたが、3Dプリンターを使うことで、部品に合わせた複雑な形状の治具を迅速に作れるようになりました。特定の部品を特定の向きにしか置けない治具を作成することで、新人作業者であっても、大きさや形状が似たような部品を誤って取出したり、組付けるミスがなくなりました。
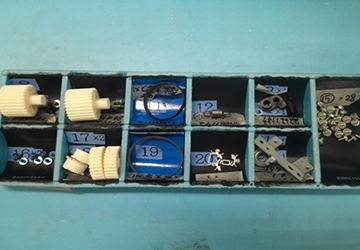
部品点数が多く、形状も似ているため、取り間違えや組付けミスの原因になっていた。
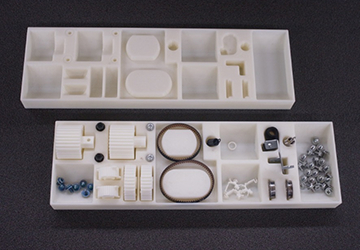
部品形状に合わせた配膳トレイ作成により、トレイ上を目視で部品のチェックができミスを防止。
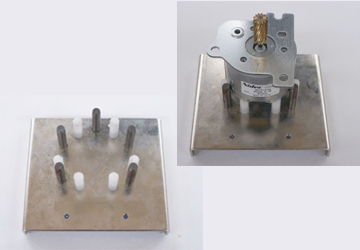
部品を組付ける向きや、順番が分かりずらいため、組付けミスが発生し易く、作業の習熟にも時間がかかる。
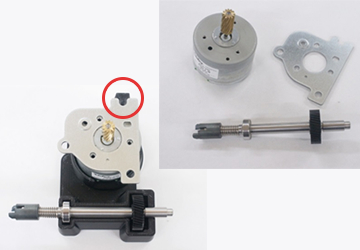
治具を部品形状に合わせ、ガイドを付けることで、見ただけで誰でも組付けが可能に。また複数治具の集約化で省スペース化。
組付け部品と工具の色分けで、『作業ミスを削減』、『消耗品コストを90%削減』
3Dプリンターを使い、色分けした治具を作ることで、「黄色いトレーから取り出した部品は黄色い治工具で組み立てる」といったことができるようになりました。色別に一連の作業が完結する工程にすることで、組立ミスを大きく減らすことができました。
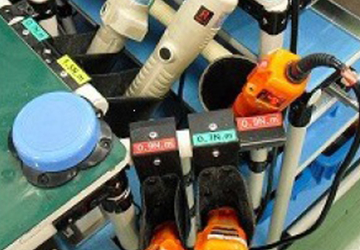
どの部品をどのトルクドライバーで締め付けるか、作業者が指示書を見ながら組立て。
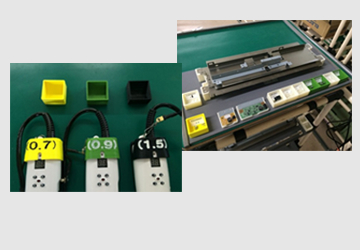
締付けるトルクドライバーの色と対応
部品トレーの色と同色のカバー色のトルクドライバーを選ぶだけで迷わずに作業できる。
治工具を樹脂製に変更し、『20分の1に軽量化』、『省スペース化を実現』
従来は主に金属性の治工具を使用していたため、相当な重量であり、作業者の安全と作業性確保のため、治工具を作業台にしっかりと固定しなければならず、生産工程の変更に対応しづらく、作業スペースを消費していました。3Dプリンターにより、プラスチック素材の樹脂の治工具に変更することで、大幅な軽量化を実現し、作業台への固定が不要となり、作業スペースの省スペース化も実現。生産工程の変更に柔軟に対応できるようになりました。
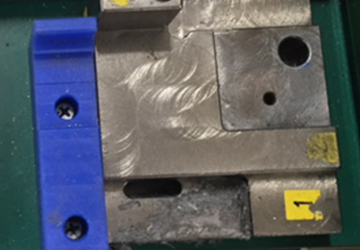
金属製で重く、安全のために作業台に固定する必要がありスペースを消費。
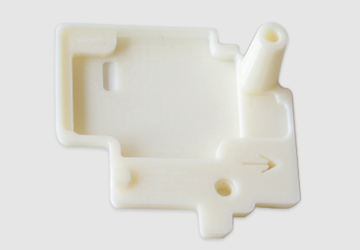
樹脂製で軽量化し、作業台に固定が不要。簡易な作業台で作業が可能となった。
治具製作プロセスの変革により、『調達納期を平均3週間 ⇒ 最短1日に短縮』
従来は治具を外部委託で製作して現場に投入していましたが、多くの製作プロセスが必要で、外注管理の手間などもあり調達納期に3週間近くもかかっていました。そのため、実際は追加工や設計変更などがあっても現場ではやむを得ず使っているということもありました。3Dプリンターによる治具製作に変更したことで、モデリングからすぐに造形することができ、設計変更などにも即座に対応できるため、調達納期が大幅に短縮できました。現場に導入した3Dプリンターで造形した場合は、わずか1~3日で対応できるようになりました。
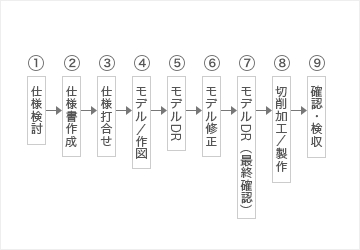
仕様検討から治具製作・確認までに多くのプロセスが必要で調達期間がかかっていた。
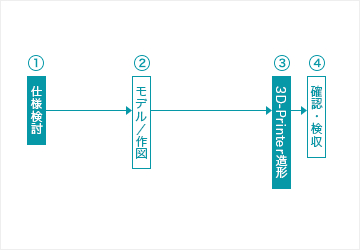
モデリングから直接造形プロセスに入れるため、治具の調達期間を大幅に短縮できた。
治具製作の改善効果を積上げて、生産ラインを再構築
さらに改善プロジェクトでは、治工具で実現した改善を工程全体に展開することで、生産ラインそのものの見直しにも取り組みました。
従来の生産ラインでは、組立てユニット毎に設けられた複数の作業台を作業者が行き来しながら組立て、専用の配膳棚にて次工程に供給する仕組みのため、作業導線が複雑で、また作業台のために多くのスペースを割く必要がありました。そこでプロジェクトでは、従来の固定の作業台ありきの考え方から大きく発想をかえ、複数の作業台と治工具を集約し、配膳棚と一体化した「移動式の作業台車」を考案しました。組付ける順番に並んだ2列の部品棚の間を作業者が移動式の作業台車を押して歩き、棚から部品を入れた治具を取り出して、ユニットを組立てて次に進む。ラインの端まで作業台車を押し進めると、全ての組立ユニットが組み上がる仕組みとなっています。これを生産ラインに導入することで、生産ライン全体で大きな改善効果が得られました。
この改善のポイントとなった「移動式の作業台車」が実現できたのは、3Dプリンターにより、部品形状に合わせた治工具が作成でき、複数治具を集約化することで省スペースができたこと、また樹脂製の治工具に変更することで軽量化ができたからこそでした。
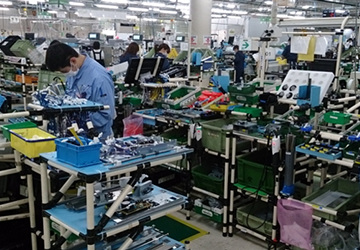
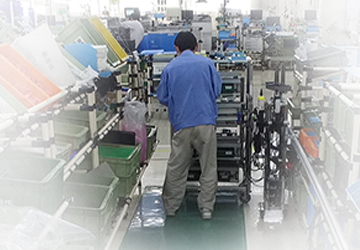
- ライン再構築により生産効率が20%以上改善
- 組み立て品質の向上により、月間不具合件数が0件
- 移動式作業台への集約で作業スペースを20%削減
- 工具数の50%削減により、工具の管理コストを大幅削減
今後の展望
3Dプリンターを活かした新しい生産方式に挑戦していきたい
3Dプリンターの導入によって、生産プロセスを根本的に見直すことができました。また、短期間・低コストで治具を作れるようになったことで、現場には様々な改善のアイディアが生まれています。今後は更に治具のレベルを高めて、『作業台を見れば品質確保がされていて第三者確認もいらない』というところを目指していきたいと思っています。
3Dプリンターを使い始めてから1年が経ち、活用のノウハウが徐々に溜まってきています。新しいものにチャレンジして、新たな課題を見つけ、その改善結果を現場にフィードバックしていくというPDCAサイクルがうまく回り始めたと感じています。今後も、様々なポテンシャルを組み合わせて、新しい生産方式などにつなげていきたいと思います。
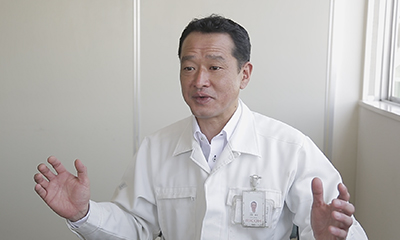