世界のトップ技術を競うモータースポーツの世界で、
開発・設計に3Dプリンターを活用。
“超”短納期、多品種少量のパーツ製作には必要不可欠な3Dプリンター!
株式会社トムスは1974年の設立以来、レース事業・デザイン事業・自動車用品事業の3事業を展開。レーシングカーの研究開発は元より、レース活動で蓄積したノウハウを活用し、あらゆる分野の製品のデザイン、設計、試作開発、他社様のコンストラクションマネジメントなどの開発補助業務まで、製品開発に関する業務を一貫して行い、モータースポーツの発展とモータリゼーションの活性化を目標に活動している企業です。繊細な部品を自由に設計し形にできる3Dプリンターは、アイデアを形にするスピードと独自性を生み出すアイテムとして活用。世界に誇れる品質と性能を兼ね備えたアイテムを、世界に向けて発信し続けています。
- 所在地:
- 静岡県御殿場市
- 主な業務:
- ・車輌デザイン 設計・製作
- ・工業製品 企画・開発
- ・試作品 企画・開発・製作
- ・3次元測定及びリバースエンジニアリング 他
- URL:
- https://www.tomsracing.co.jp/sv/tomss-design/index.html
レーシングカー設計はスピードが求められ、数十種類のパーツを少量で製作するため3Dプリンターは欠かせない存在
レース車両開発日程に合わせて、短納期で多岐にわたる分野(空力、構造、機構等)の設計を行っています。設計終了後には即座に製作を行うため、3Dプリンターで部品製作することを前提に設計を進めています。また「3Dプリンターならではの設計を行い、従来工法ではできなかった複数部品の一体化により設計工数が大幅に削減でき、弊社では3Dプリンターは欠かせない存在です。
部品が製作できた
でき、パーツ点数も設計工数も削減できた
3Dプリンターで製作した部品(一例)
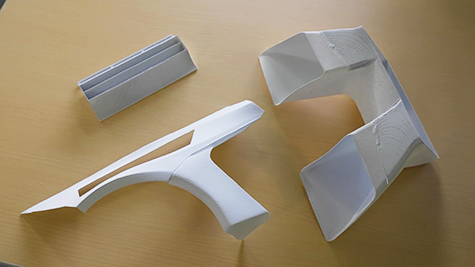
風洞試験用の部品
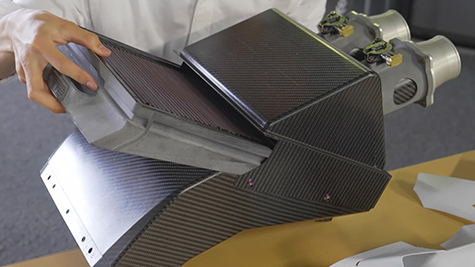
エアクリーナーボックス
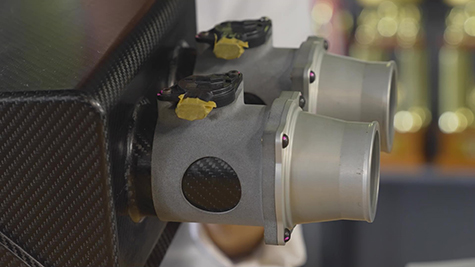
センサーブラケット
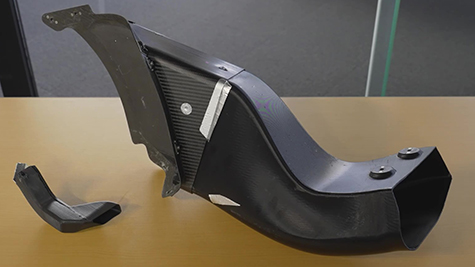
ブレーキ冷却用のダクト
導入した機器/サービス
レース車両開発の日程に合わせて短納期で数十種類のパーツを少量で製作する必要があり、見積回答が早い点、また造形物や用途に合わせて造形方式・造形材料、納期を短縮する方法を技術者から提案してもらえるため、リコーの「3Dプリンター出力サービス」を利用しました。
お客様インタビューCustomer Interview
株式会社トムス
デザインセンター デザイン事業部
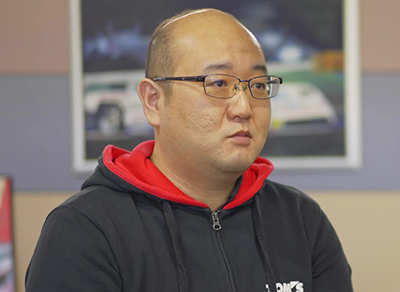
- 設計課
- 田坂 紘一様
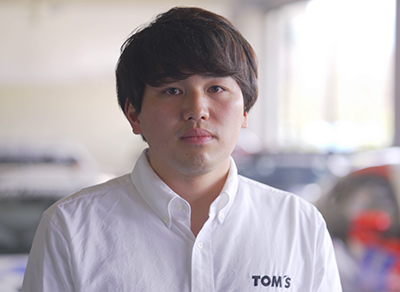
- 設計課
- 市野 雄麻様
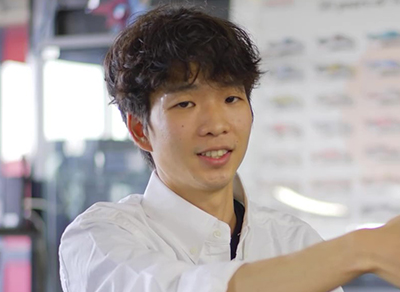
- 設計課
- 田畑 直樹様
背景・課題
3Dプリンター前提で設計
設計分野は多岐にわたりまして車一台まるごと全てを設計していると言っても過言ではありません。例えば外装部品や空力部品、ロールケージの設計、その他サスペンションや操舵装置に関しても我々は設計を手掛けています。2007年にデザインセンターでも3Dプリンターを導入し、試作検討用のモックアップや製作用治具の製作のために使用していました。3Dプリンター前提で設計を進めておけば寸法や公差などを記入した2次元図面を作成する必要もなく、設計担当者が設計を終えると3Dプリンターにデータを流せば、すぐに製作に入れるのはとても魅力的でした。
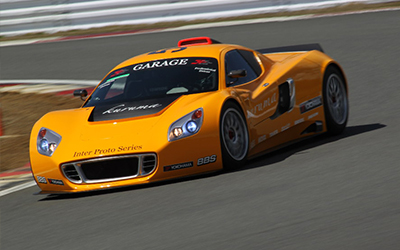
出力サービスの活用について
リコー出力サービスの造形だけではない技術サポートにより工数削減
現在は保有していた3Dプリンターのメーカーサポートが終了して交換部品が入手できなくなり、自社での運用はしていません。しかし3Dプリンターは治具製作や短納期で製作するためには必要不可欠であったために試作業者さんへ製作を依頼していましたが、使用したい3Dプリンターを調べてお願いしても希望材料が対応していなかったり、納期やコストなど条件が合わず苦労していました。かなりタイトな納期の中で発注先を探す状況において、リコーさんは使用したい3Dプリンターや材料も対応でき、すでに取引口座もあったので事務処理もスムーズでした。リコーさんは見積回答が早い点や、造形物や用途に合わせて造形方式や造形材料の提案、急いでいる場合は納期を短縮する方法を提案頂けるといった点が魅力です。また、空力検討の初期段階では形状を確定しきれないため、厚みのないサーフェスモデルで設計を進めていくことが多いのですが、複雑な3D曲面の場合、簡単に厚みを設定できない場合もあり作業工数をとられていましたが、リコーさんに厚み設定まで対応して造形してもらえるので、大幅な工数削減につながりました。
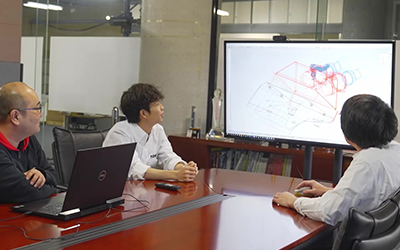
3Dプリンター活用メリット
設計時間の短縮・自由度の高い部品設計
非常に短納期な仕事が多く、少しでも日程が遅れるとレーシングカーの試験走行の日程に間に合わなくなったり、他システムとの部品の連携テストが行えなかったりという、スピード重視な業界です。たとえば風洞試験では1回に数十個の部品を作る上に、試験と試験の間隔がとても短いため、短期間で多品種の部品が作れる3Dプリンターの存在は欠かせません。
レーシングカーのフロントブレーキに空気を送り込むための冷却用のダクト(写真①)は、CFRP(炭素繊維強化プラスチック)で製作する場合は型設計が複雑化し、その分設計に時間が取られてしまいますが、3Dプリンターであれば三次元曲面で複雑形状でもそのまま作れます。もう一つのメリットは、一体造形でパーツ点数を少なくできる点です。すべてCFRPで製作すると、車がクラッシュしたときにタイヤやホイール、ブレーキを痛めない様に吸収する構造を考案し、CFRP以外の樹脂製のつなぎを作る必要もあります。一つの部品で完結できたのは3Dプリンターだからこそだと思っています。
他にも3Dプリンターだから作れる形状を多く設計しています。例えばエアクリーナーボックス(写真②)という部品は、中のエアフィルターを簡単に交換できるようカートリッジ式に変更してはどうかというアイデアが出ました。3Dプリンターで試作品を造形したのですが、設計の自由度が非常に高いため、直感的に設計することができ、リブの構造や装着時のツメの構造まで一体で造形できるので、開発がとてもスムーズに進みました。
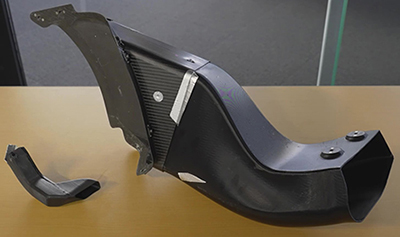
【写真①】ブレーキ冷却用のダクト
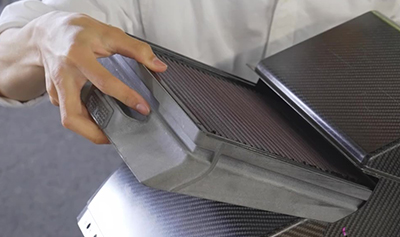
【写真②】カートリッジ式エアクリーナーボックス
今後の展望
スピードと安全を同時に求められるレーシングカーや、燃費の向上を期待される乗用車や電気自動車においても、軽量化はこれから重要なテーマの一つです。従来の製造方法とは全く異なり、デザイナーのアイデアを活かした自由な形状を作れる3Dプリンターは、これまで実現できなかった更なる軽量化を可能にしてくれると思っています。そういう観点からも、3Dプリンター技術の進化にも私達は期待しています。