3Dプリンター出力サービスサポートオプション
工業模型造形
概要
工業製品の企画開発・設計においてデザインプレゼンや完成品のイメージ確認、教育現場などでは、イラストや設計図に加え、模型があるときの訴求力や理解力は飛躍的に高まります。昨今、工業模型の制作については、切削等の従来工法と比較して、より複雑な形状を短納期で造形できる3Dプリンターによる模型造形のニーズが高まっています。一方、3Dプリンターで模型造形をしようとした場合、どのような造形方式と材料を使ったらよいのか?モデルを縮尺する場合、肉厚はどうしたらよいのか?1回で造形できないような大型模型を作成するにはどうしたらよいのか?といったような様々な課題に直面します。本オプションサービスでは、工業模型造形において3Dデータ作成から造形に至るまでに生じる様々な課題を3D造形専門の技術者がトータルでサポートし、お客様の目的・用途に応じた最適品質の模型を短納期で提供するサービスです。
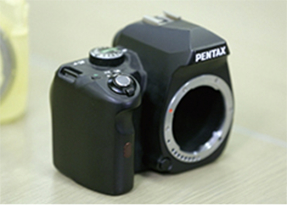
工業模型造形の活用例
- ・展示会やショールームに展示する自社製品の模型
- ・ビルなどの建築構造物の完成イメージ模型
- ・建築物の工事段取りの打ち合わせのため、部分的な構造模型
- ・プレゼンテーションや教育のための構造模型
実施内容(一例)
工業模型造形オプションサービスでは、工業模型造形において3Dデータ作成から造形に至るまでに生じる以下のような様々な課題をトータルでサポートします。
造形方式や材料がわからない
模型造形専門の技術者が、お客様から模型の目的や用途を詳細にうかがった上で、要求品質を満たす最適な造形方式・材料・二次加工処理などをトータルでご提案します。
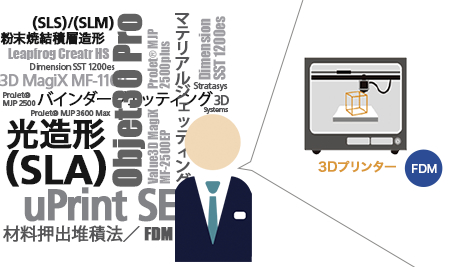
原寸を変えて造形したい
お客様からお預かりした3Dモデルを原寸から3Dプリントの造形サイズに最適となるように修正致します。サイズの縮小に伴って薄肉化した部位の修正や、造形に必要な部分のみのデータ切り出しにも対応します。
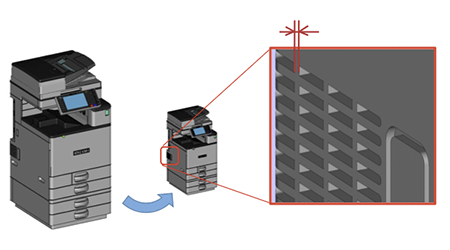
大型の模型を作りたい
一回の造形で900mm×600mm×900mmまで対応可能ですが、さらに大きい場合はモデルを分割して接着することも可能です。最適な分割面を検討・提案し、大型の工業模型の作製にも対応します。
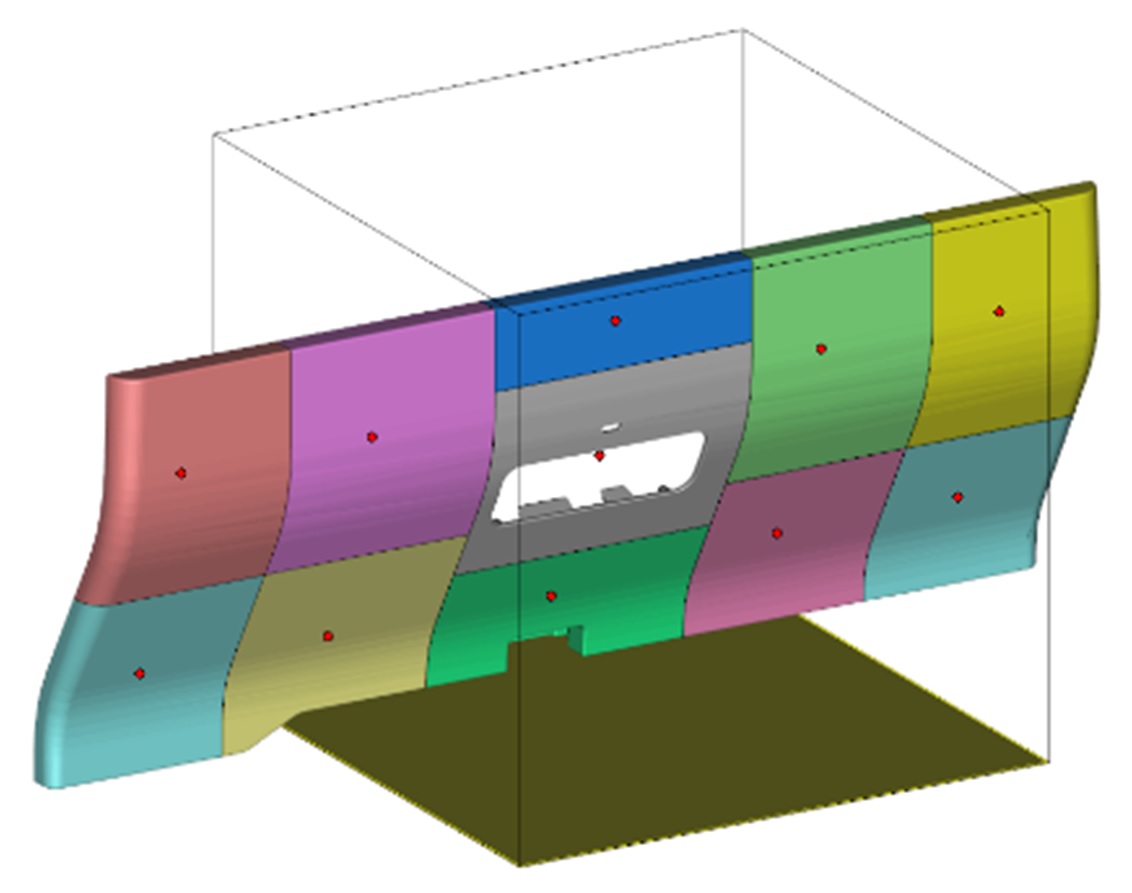
モデル分割のシミュレーション
完成品に色を付けたい
磨きや塗装といった二次加工まで受付可能です。お客様から造形品への配色をヒアリングし、可能な限りご要望の色に仕上げます。マテリアルジェッティング(MJ方式)やバインダージェッティング(方式)は、予め造形時に色を付けることも可能です。
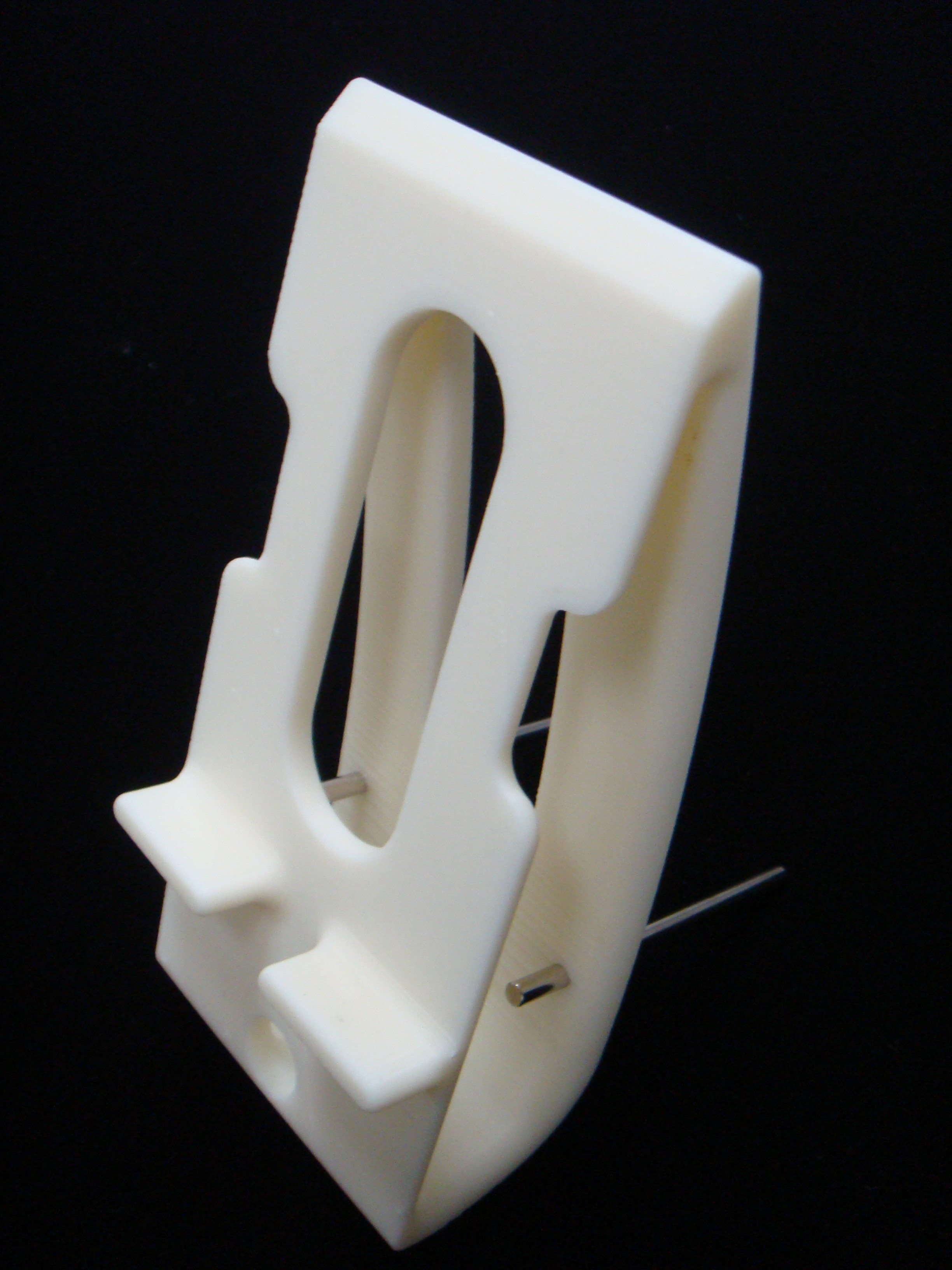
塗装前
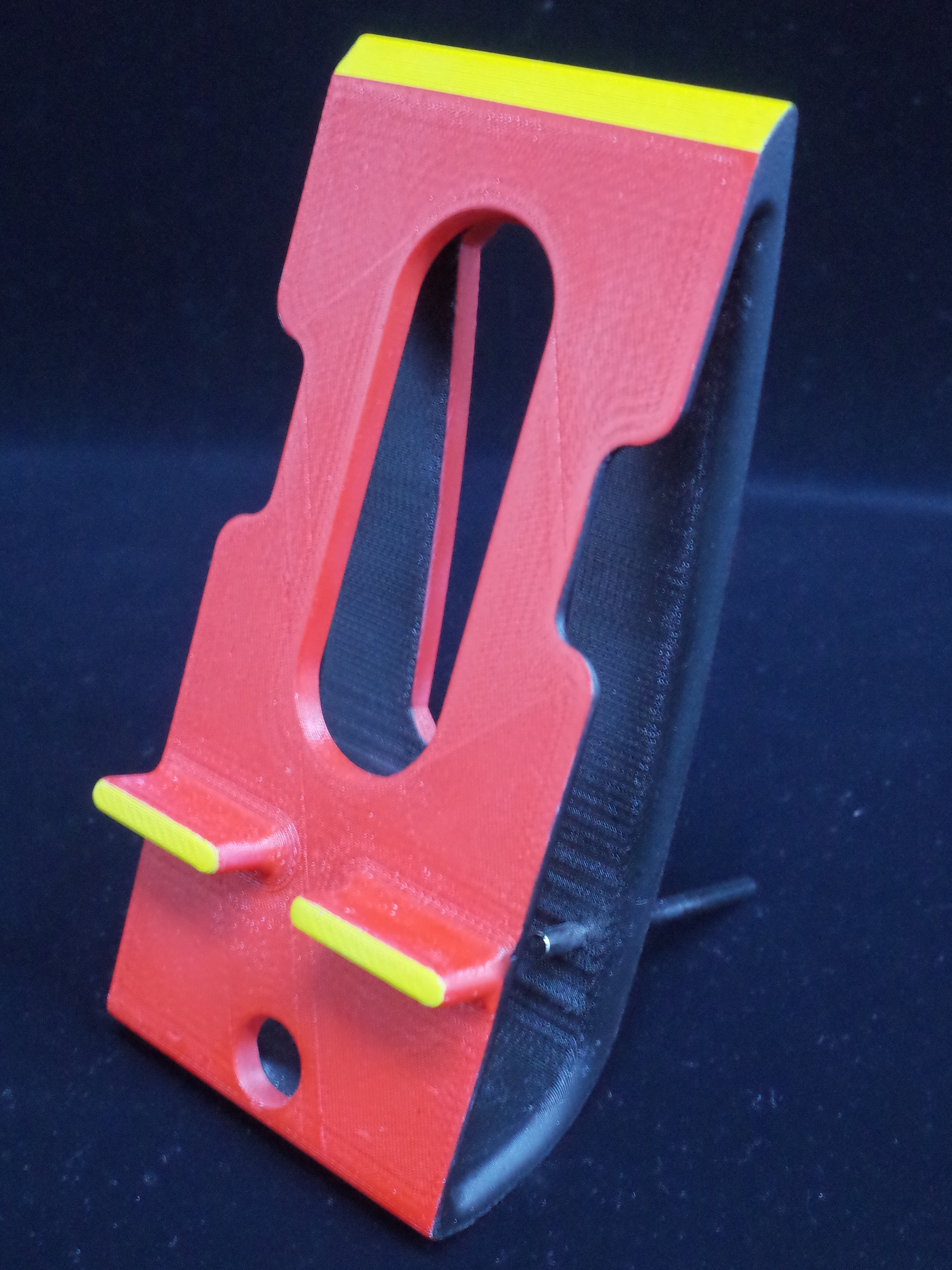
塗装後
模型造形例
工業模型造形オプションサービスでは、工業模型造形において3Dデータ作成から造形に至るまでに生じる以下のような様々な課題をトータルでサポートします。
-
PENTAXブランド(カメラボディ)の模型
-
田瀬ダム(岩手県花巻市)の模型
-
樽井樋門(茨城県常総市)の模型