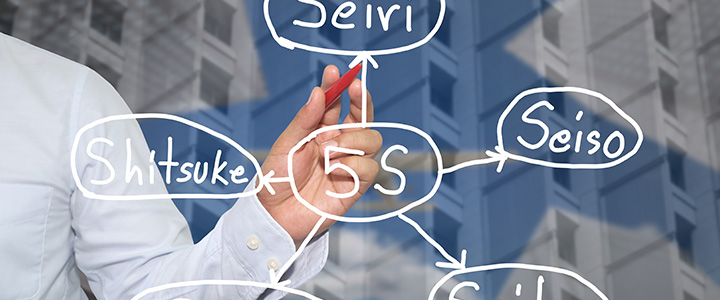
職場環境の話の中で「5S」という言葉によく出会います。5Sは職場環境の改善にはじまり作業の効率化などにもつながる活動であり、企業に大きなメリットをもたらしてくれます。
この記事では、5Sに取り組むべき理由のほか、実践していくうえで必要となるポイントや進め方について解説します。企業のご担当者様はぜひ参考にしてみてください。
目次
5Sとは
5Sとは「整理・整頓・清掃・清潔・しつけ」の5つの活動のことで、読み方は「ゴエス」です。この5つをローマ字で書くとすべてSで始まるため5Sと呼ばれます。
それぞれの具体的な内容は以下のとおりです。
整理 | ものを仕分けして不要なものを処分し、必要なものだけ残すこと |
---|---|
整頓 | 必要なものを使いやすいように整えて配置すること |
清掃 | 環境や機械のごみや汚れを取り除いて、点検すること |
清潔 | 整理・整頓・清掃の行き届いた状態を保つこと |
躾 | 整理・整頓・清掃・清潔を習慣づけること |
5Sがいつ始まったかには諸説ありますが、昭和30年代に自動車メーカーのトヨタが始めたという説が有力です。当時トヨタが、必要なものは必要な時に必要な量だけ供給するという「ジャスト・イン・タイム」を導入する際に始まったといわれています。
5Sの重要性
5Sは単に片付けたり掃除したりすることではありません。5Sを徹底することによって、とくに製造業において重要となる「QCD(品質・コスト・納期)」の改善・向上に役立つとされています。
そのほか従業員による作業の効率や仕事に取り組む姿勢の向上などの効果もあり、そういったヒトにかかわる面からも会社経営によい影響を与えます。
このように5Sはヒト・モノ両面においてよい影響をもたらします。
5Sの目的
5Sの主な目的は、作業環境を整理整頓し、生産性と効率を向上させることにあります。
「整理・整頓・清掃・清潔・躾」の5つのステップを通じて、作業場の無駄を排除し、作業効率を高めるために行われます。整理では不必要な物を排除し、整頓では必要な物を適切に配置します。清掃と清潔によって作業環境を常に清潔に保ち、躾でこれらの活動を習慣化します。
5Sのプロセスにより、事故のリスクを減らし、作業の安定性を高めると同時に、作業者のモラルと生産性を向上させる効果があります。
また、5Sは品質管理の基礎となり、製品やサービスの品質向上にも寄与します。5Sは、単なる掃除や整理にとどまらず、組織の文化として根付くことで、継続的な改善と効率的な運営を促進します。
5Sのメリット・デメリット
5Sの導入には多くのメリットがあります。まず、整理整頓された作業環境は効率を大幅に向上させます。必要な道具や資料がすぐに見つかり、時間の節約につながります。
また、クリーンで整理された環境は安定性を高め、作業場での事故リスクを減少させます。これは、特に物理的な危険が伴う製造業において重要です。
さらに、整理整頓は品質管理にも効果的で、製品やサービスの品質向上に寄与します。
しかし、5Sの実施にはいくつかのデメリットも存在します。最も大きな課題の一つは、全員の協力と継続的な努力が必要であることです。初期の段階での組織全体のコミットメントがなければ、5Sの導入は困難になります。
また、過度な整理整頓は、場合によっては逆に作業効率を低下させる可能性があります。極端な整理整頓は、必要な物が見つからなくなる原因となることもあります。
このように、5Sの実施は、多くのメリットがある一方で、デメリットもあります。効果的に5Sを実施するためには、これらのポイントを理解し、適切に対応することが必要です。
製造業の企業が5Sに取り組む理由
製造業の多くの企業が5Sに取り込んでいる理由、あるいは5Sに取り組むべき理由としては、次の4つが挙げられます。
● 作業効率を向上させるため
● 従業員の意識向上に繋げるため
● 現場の安全管理を徹底するため
● 組織の意識統一を図るため
1つずつ見ていきましょう。
作業効率を向上させるため
まず製造業の場合、5Sに取り組むことで作業効率が向上します。 資材や道具が定位置にあると、探しものをするムダな手間と時間がかからなくなります。モノもなくならないので、紛失に対処する労力や時間も不要です。その結果最低限の必要な作業だけで済むようになり、作業効率が向上するのです。
さらに作業効率が向上すれば、短い時間・労力で同じ結果が出せたり作業の品質が保ちやすくなったりします。その結果、生産性や利益率のアップにもつながります。QCDの向上につながるのはこのためです。
関連コラム:ポカミスとは?製造業におけるポカミスの原因と対策
従業員の意識向上に繋げるため
5Sを徹底することが従業員の意識向上にもつながるのも、5Sに取り組むべき理由の1つです。
たとえば5Sによって現場の環境が改善されると、整った良質な状態が基準となります。そうなると、ゴミが落ちていれば拾い、乱雑な状態になっていれば元に戻すようになるでしょう。整った状態を保つ気持ちが生まれるのです。
このように5Sによって規律を守ろうという意識が高まり、従業員全体の意識が向上することを期待できます。
現場の安全管理を徹底するため
5Sを徹底することは安全管理にもつながります。
5Sによって、資材や道具が整頓された状態、作業場の清掃が行き届いた状態、設備の点検がされている状態が保たれます。
たとえば使いかけの資材や道具が床に直置きされていない、設備に油汚れや粉じんがない、作業機器が安全に作動するなどです。
職場が整理整頓の行き届いた清潔な状態に保たれていると、安全管理しやすくなって、事故のリスクを減らすことができます。
関連コラム:工場の安全対策とは?対策のポイントと事例をご紹介
組織の意識統一を図るため
5Sの徹底は、意識統一やチームワークの向上をもたらします。
5Sを推進するためには、同じ価値観や方法を共有・実行しなくてはなりません。
つまり、5Sの導入・推進の過程でメンバーにルールを守ろうという意識が高まることとなります。その結果、意識が統一されることやチームワークが向上することが期待できます。
製造業における5Sの具体的な効果
製造業において5Sはどうのような効果かあるのか、「PQCDSM」と「QCD」を例に解説いたします。
1. PQCDSMの向上
PQCDSMは、製造業やその他の業界で品質管理やプロセス改善の指標として用いられるアクロニムで、以下の要素を指します。
P: Productivity (生産性) - 効率的に商品やサービスを生産する能力。高い生産性は、少ない入力(例えば、時間、資材、コスト)でより多くのアウトプットを生み出すことを意味します。
Q: Quality (品質) - 製品やサービスが顧客の要求や期待を満たす度合い。高品質は顧客満足度を高め、リピート購入やブランドの評判向上に繋がります。
C: Cost (コスト) - 製品やサービスを提供するのにかかる費用。コスト管理は、無駄を削減し、効率的な資源の使用を意味し、利益の最大化に貢献します。
D: Delivery (納期) - 製品やサービスを顧客に提供するスピードや時間。迅速な納期は顧客満足度を高め、競争優位性を確保します。
S: Safety (安全) - 製品の使用や製造プロセスが従業員、顧客、社会に対して安全であること。安全性の確保は、法令遵守だけでなく、企業の社会的責任を果たす上で重要です。
M: Morale (士気) - 従業員の働く意欲や満足度。高い士気は生産性の向上、人材の定着、ポジティブな職場環境の創出に繋がります。
PQCDSMは、企業が経営目標を設定し、達成するための具体的な指標として活用されます。PQCDSMの各要素を継続的に監視し、改善することで、企業は競争力を高め、持続可能な成長を実現することができます。
これらの要素を大きく改善するマネジメント手法として、5Sは極めて効果的です。例えば、整備された環境は安全を確保し、整理された工程は生産のスムーズな流れを実現し、コスト削減に繋がります。また、整頓された作業場は士気を高め、品質の向上にも寄与します。考え方やノウハウを集め、その他の改善手法と組み合わせることで、PQCDSMの向上に大きく寄与します。5Sは単なるきれいな職場づくりのためだけではなく、会社の文化として根付かせることが重要です。
2. QCDの実現
QCD(品質、コスト、納期)は製造業における重要な経営指標で、QCDの要素を改善するために5Sのマネジメント手法が用いられます。意味のある改善を実現するために、5Sは具体的な活用方法であるきれいな職場環境の維持を通じて、しまうべきものの明確化、必要なものがすぐに取り出せる体制の構築が必要です。これにより、作業効率が向上し、在庫の過剰保有を防ぐことができます。また、ミスを減らし、出荷の遅延を少なくし、最終的に顧客満足度を向上させます。
5Sは人材育成にも寄与します。考え方を整えることで、従業員は自らの作業環境をきれいに保ち、集中力を高めることができます。これは品質(Q)の向上に直結し、コンテンツの品質保証に繋がります。従業員が自分の作業環境を管理することで、自身の業務効率だけでなく、会社全体の生産性が向上します。
さらに、5Sの原則に従って整理整頓された環境は、安全性を高めることにも寄与します。安全な職場は、事故や故障が少なくなり、結果としてコスト削減(C)に繋がります。
また、5Sは在庫管理にも大きく影響します。適切に整理された物品は、必要な時にすぐに取り出せるため、無駄な在庫を減らし、保管場所を確保することができます。これは、納期の厳守に直接的に寄与します。(D)
5Sを徹底する際のポイント
次に、5Sを徹底する際にポイントとなる事項について解説します。具体的には次の3点が挙げられます。
● チェックシートを活用する
● 5Sを徹底するメリットを社内で共有しあう
● 5Sのルール決めは現場の従業員の意見も組み込む
上記3点は、標準化や共有をしながら徹底を進めること、それを続けられる仕組みを作ることだといえます。1つずつ見ていきましょう。
チェックシートを活用する
チェックシートを使うと、5Sの徹底につなげやすくなります。5つのSそれぞれについて具体的な項目を設定し、どのレベルを求めるか言語化・数値化します。〇×式にしたり5段階評価にしたりするなど、自社の状況などに合わせて使いやすいシートを作成しましょう。
チェックシートを作成することで、基準が可視化されます。その結果、意識も評価基準も標準化・統一され、徹底を進めやすくなります。
それぞれのSについて項目の例を挙げておきます。
整理:不用品は所定の場所に置き、はっきり表示されている
整頓:棚やキャビネットには品名や管理担当者が表示されている
清掃:使用する機械・設備は清掃・点検されている
清潔:機械設備に油汚れ・粉じんの堆積がない
しつけ:定期的に上記清掃など行っている
チェック項目の例やテンプレートが厚生労働省などによって提供されています。既存の例を自社用にアレンジするとよいでしょう。
5Sを徹底するメリットを社内で共有しあう
5Sによって得られるメリットは社内で共有しましょう。
5Sの導入自体が目的化してしまっていると、5Sの徹底を長期的に継続することができなくなりがちです。
メリットを共有することで、取り組みの持つ価値を理解することができるようになります。継続するモチベーションを保つこともできるでしょう。
5Sの導入時はもちろんですが、形骸化するのを避けるためには、定期的にメリットを確認することが有効です。「どのようなメリットが得られるか」だけでなく、「どのように改善されたか」という、実際に得られたメリットも共有しましょう。
5Sのルール決めは現場の従業員の意見も組み込む
5Sのルール決めは、現場の従業員の意見を組み込むことが大切です。
トップダウン式だと、現場が納得して取り組みにくくなってしまいます。あるいは現場に即していない机上の知識だけでルールを決めると、作業しにくくなり習慣化されなくなりがちです。
整理や整頓のルールは、現場の従業員でないと効率がよくなる内容がわかりません。現場の環境に合わせるよう、現場の意見をもとにルールを決めましょう。交代制などで全体参加のミーティングが行いにくい場合は、アンケートやメール、チャットツールなどで意見を集めるとよいでしょう。
5Sの進め方
次に、実際に5Sを進める手順について解説します。5Sに取り組むべき理由・目的は、すでに述べたように作業効率の向上・従業員の意識向上・安全管理・組織の意識統一などです。これらを実現できるように意識しながら進めていきます。
【5Sの進め方】
1. 5Sに取り組む目的を明確にする
└「不良品発生率〇%以下」など数値化して目標の形で示すと理解しやすい
2. 明確化した目的を社内で共有する
└ミーティングなどで確認するほか、導入後は共有部分や作業場にも掲示する
3. 業務プロセスの可視化によって、5Sの最終的なイメージ像を明確にする
└現在の業務プロセスと、5S徹底後の業務プロセスの両方を可視化。現在のプロセスは課題の発見に役立つほか、どれだけ改善できたかを測る基準になる。5S徹底後のプロセスはゴールを示す
4. 5Sの活動計画に沿って取り組みを実施
└実行に移す順序は、整理→整頓→清掃→清潔→しつけの順にする。PDCAで改善を積み重ねる
5Sがうまくいかない原因と対策
5Sがうまくいかない原因と、それぞれの対応策を見ていきましょう。
1. 物の置き場が定まっていない
物の置き場が決まっていないと、どこに何があるのか分からず、無駄な時間を使ってしまいます。
└対策としては、物の「定位置」を作り、それを全員で共有することが重要となってきます。
2. 使ったものをすぐに片づけない
使用後の物をすぐに元の場所に戻さないと、次にそれが必要なときに探す手間が発生します。
└対策としては、使用後は必ず元の場所に戻す、という行動を徹底することが重要です。
3. 人によって保管方法が違う
同じ物でも人によって保管方法が違うと、探す時間が増え、作業効率が下がります。
└対策としては、保管方法を統一し、それをルールとして定着させることです。
4. 5Sを継続しない
5Sは一度行ったからといって終わりではなく、継続して行うことで効果を発揮します。
└対策としては、定期的に5Sの活動を行い、それを習慣化することで5Sが定着し効果を最大限に引き出すことができます。
どの問題も基本的な行動の積み重ねが解決の鍵となります。5Sをうまく活用し、より良い職場環境を作りましょう。
整理・整頓に役立つ『RICOH らくらくKAIZENサービス』
5Sへの取り組みには、「RICOH らくらくKAIZENサービス」をツールとして活用するのがおすすめです。
5Sに取り組む際には、まず始める前の現状把握が非常に重要になります。自社固有の課題を発見するために必須だからです。また現状把握によって課題を把握しルールを策定して取り組みを始めたら、今度は継続的にPDCAを行っていくために日常的な課題の発見が大切となります。
そのいずれにも、RICOHらくらくKAIZENサービスが役立ちます。改善点に気づいたら、その場でスマートデバイスで写真を撮影、テンプレートに合わせて文章を作成して報告できます。課題点を蓄積しやすいのでルールを決める際にも有益です。さらにアプリ上で上司の承認や改善指示も可能なので、PDCAを回す際の課題解決の迅速化が可能です。
詳しくは以下のリンクからご確認ください。
まとめ
5Sの徹底は、製造業の企業が職場環境を改善して自社の生産性を向上させたり企業風土を変革していったりするために有効です。結果的に自社の競争力を高めることにもつながります。
5Sによる成果を得るためには継続的に取り組むことがポイントとなります。5Sを継続するためには、日常的な取り組みの負担を減らすことが必要です。負担を削減するためにはツールの活用がおすすめです。自社に合うツールの導入を検討してみてはいかがでしょうか。