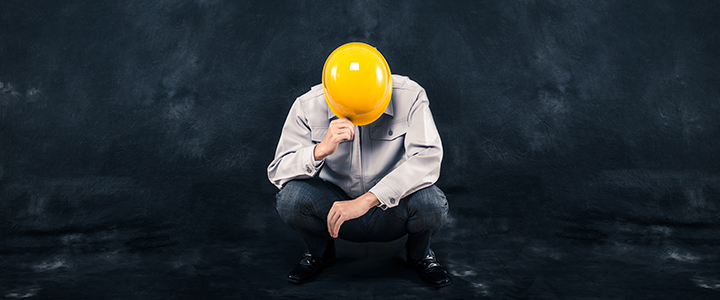
製造工程における作業ミスには多くの種類があり、その原因をさまざまです。影響の小さいミスもありますが、中には大きな影響を及ぼすものもあるでしょう。たとえ些細なミスでも、放置しておくと気が付かない間に問題が大きくなる場合もあります。
製造業における作業ミスの代表的なものの1つが「ポカミス」。本コラムではポカミスとはどのようなものか、またその原因および対処方法について、実例を交えて解説します。ポカミス対策に課題をお持ちのご担当者はぜひ参考にしてください。
ポカミスとは
「ポカミス」とは元々は囲碁や将棋の用語で、「普通なら考えられないような悪い手を打つ」ことを意味し、「ケアレスミス」と言い換えられることもあります。製造業で用いられる場合は、「不注意などで引き起こされるさまざまなミス」のことを指します。ポカミスには、受け入れ時の伝票や作業指示書の見間違い、ピック時の部材の選択間違いや数量間違い、設備操作における異物・異機種の混入、組み立て時の治工具などのセットミスや調整ミス、作業飛ばし・行程飛ばし・作業間違い、機械操作ミス、さらに検査時の見逃しや過剰検出など、各工程によってさまざまなものがあります。ポカミスが製品の不良や製造設備の故障・作業事故、さらには取引先からのクレームなどの発生原因となるケースも少なくありませんので、極力発生させないような対策を講じることが重要です。
製造業でポカミスが発生する原因
ポカミスの原因には主にヒューマンエラーによるものと作業・設備環境によるものがあります。不注意や見落とし、勘違い、失念などのヒューマンエラーによって「指示内容を間違う・忘れる」「製造設備の操作ボタンを見間違える」「必要な手順を飛ばしてしまう」「検査項目を他の製品の項目と間違える」などのミスが発生する恐れがあります。
これらによって、異品や異物の混入や、間違った方法で組み上げてしまう誤組、加工しなければならない箇所が漏れる未加工、さらに欠品などのトラブルが発生する恐れがあります。ヒューマンエラーによるポカミスは、当事者本人の自覚がない場合やその場で修正してしまう場合があるので、問題として認識できないケースもあるので注意が必要です。
ヒューマンエラー以外に、作業環境や設備環境が原因となる場合もあります。例えば作業現場で工具や部品が整理されずに乱雑に置かれていては、ミスも起こりやすく作業効率も上がらないでしょう。またそれらが取りやすい場所に配置されていなければ落下して破損させたり、作業員が怪我を負ったりする恐れもあります。
さらに、作業場が暗く過ぎる場合は当然ミスも多くなります。また、暑すぎたり寒すぎたりしては汗で手元が滑ったり、思うように力が入らなかったりすることがあり、集中力も鈍ってしまいます。製造設備が原因となるポカミスでは、違った機能や正反対の機能を持つボタンの形状が似ていると押し間違いが発生しやすくなったり、操作方法が非常に複雑な設備の場合に慣れるのに時間がかかり、ミスする確率も上がったりするケースがあります。
製造業のポカミスを防止するための対策とは
製造業のポカミス対策で必要なステップは以下の5点です。
①原因特定
②作業手順の変更、設備や作業環境の改善
③マニュアルへの反映
④対策内容の周知・徹底
⑤効果検証
ポカミスが発生する原因はさまざまです。従って、ポカミス対策でまず必要なのは、その原因を明確にすること。ポカミスはヒューマンエラーによるものが多いため、すべて人によるものと判断しがちです。
しかし上記のとおり作業環境や設備環境によっても発生するため、その点を踏まえて原因分析することが必要です。また、同じヒューマンエラーでも、作業上のミスによるものか指示などを正しく理解できていなかったことによるものかによってその後の対策が大きく異なりますので、できるだけ精度の高い作業分析と原因特定を行うことが重要です。
原因が特定できれば、そのポカミスを発生させないように作業手順を変更したり新たに手順を定めたりします。例えば作業ミスが多い箇所で新たに確認プロセスを入れる、指示内容が確実に伝わるように文書などで伝達するようにするなどの例が考えられます。手順を変更・作成した場合は必ずマニュアルなどに反映し、「誰が行っても同じ結果」になるような環境を整えておきましょう。作業・設備環境が原因の場合は、対象となる環境や設備を改善します。具体的な対策は原因によって千差万別ですが、具体的にどのような改善内容が効果的なのかは、作業テストなどを実施して判断するのも有効です。
原因特定および対策を講じた後は、その内容を作業者をはじめ関係者全員に周知徹底することが必要です。作業手順や環境などを変更した場合は、変更後の手順などに問題がないかどうかの検証も併せて実施したほうが良いでしょう。また、日頃から作業手順などが正しく守られているかをチェックすると共に、作業員のポカミス防止への意識向上を行うことも重要です。
製造業のポカミスの種類別対策
前述の通り、製造業のポカミスは大きく分けると、人によるものと作業環境や設備環境によるものに分けられます。原因に対して適切な対策を行うことで、ポカミスを防止する体制づくりを進めていきましょう。
ヒューマンエラー
ヒューマンエラーは、人間がうっかりと起こしてしまう行為が、意図しない結果をもたらすことで、「やるべきことをやらない」または「やってはならないことをする」といった行為により発生します。単純な数値入力ミスやピッキングミス等がこれに当たりますが、こういったヒューマンエラーを防ぐためには以下のようなことを意識して、職場の体制づくりをすると良いでしょう。
1)人が間違えないように人を訓練する。
2)人が間違えにくい仕組み・やりかたにする。
3)人が間違えてもすぐ発見できるようにする。
4)人が間違えてもその影響を少なくなるようにする。
これらを実現させる具体的な対策例としては、指差呼称の徹底やロボットの導入による作業の自動化などがあります。
指差呼称は意識レベルを上げ、確認の精度を向上させる有効な手段として厚生労働省も推奨していますので、取り入れていない場合はぜひ検討してみて下さい。
また、ロボットの導入による作業の自動化は根本的に人の手の作業を削減することにつながります。初期投資は必要ですが、ヒューマンエラーをゼロにすることも可能ですので、有効な手段となり得ます。
作業環境や設備環境
作業環境は主に騒音や5Sの乱れ、設備環境は主に設備不良等が挙げられます。特に、着手しやすい対策として、5Sの乱れの是正から取り組むことをお勧めします。5Sとは「整理」「整頓」「清掃」「清潔」「しつけ」の頭文字をとったものです。これらを改善することで、現場が整理整頓され、設備メンテナンスにまで目が行き届くような効果が期待できます。ヒューマンエラーの防止にもつながりますので、ぜひ実践してみてください。
画像認識技術でポカミスを防止
ポカミスは、最新のデジタル技術を使って効率良く防止することもできます。当社が開発した作業支援カメラシステム「RICOH SC-10A」(以下、SC-10A)は、画像認識技術を活用した画像のパターンマッチングによって、類似部品や欠品、作業順序などの組み立て状況を自動でチェックするカメラシステムです。
画像チェックでOKにならなければ次の作業に進めることができないため作業ミスを抑制でき、経験の浅い作業員でも安定した品質で、しかも効率良く作業を進めることができます。カメラ本体にアプリケーション類もすべて内蔵するオールインワン形態のため、モニターやキーボードなどを準備するだけで導入可能。作業中に部品のシリアルナンバーや組み立て状態の画像、作業時間などを自動収集できるので、ITによる作業分析とトレーサビリティを実現し、製造現場のDXに貢献します。
ピッキング工程における部品の過不足や類似部品のチェック、組み立て工程における作業手順や欠品チェック、検査工程における取り付けミスなどの一括チェックなど、さまざまな製造工程に適用することでポカミスを防ぎます。
ポカミス対策の事例紹介
最後に、SC-10Aを実際に製造現場に導入してポカミスを削減した事例をご紹介します。
1件目は医療機器メーカーの富士フイルムテクノプロダクツ株式会社様の事例です。同社が取り扱う医療機器の製造は、主に熟練工が担ってきました。しかし昨今人材の入れ替わりが徐々に多くなり、熟練工以外の作業員にもその製造工程を担ってもらう必要が生じてきました。
同社ではこのような課題の解決を目的に「不良の原因となる作業ミスを減らし人に依存しない仕組み」を作ることを決定。SC-10Aを導入し、血液検査装置に使用するインキュベーターユニットの製造工程における「ネジ締めの順番」、および「ネジ締めトルク」を自動で確認できる仕組みを構築しました。工程を間違えた時点でNGであることが知らされ、作業を進めることができないので作業ミスは100%削減。作業ミス防止に使っていた注意力や労力を他に使うことで作業効率向上や品質維持にも貢献しています。
次にご紹介するのは株式会社小野測器様の事例です。
各種計測機器を製造する同社では、ポカミスの撲滅と作業者個人へ依存することのない製造体制の構築という課題を抱えていました。そこで、同社製品「O-Solution DS-5000」の組み立て工程にSC-10Aを導入し、トルクドライバーと連動させてビス締めの締め忘れを検出する仕組みを構築。さらにトルクアップ信号を記録しておくことで、規定のトルク値でトルクアップされたかどうか検証できるようにトレーサビリティを向上させました。従来管理者が確認しなければならない工程をSC-10Aに置き替えることで必要なポイントで漏れなくチェックできるようになりました。さらに特定の作業員に依存することなく複数の作業員でも同様の作業を実施できる体制が整いました。
導入事例の詳しい内容は下記よりぜひご確認ください。
「RICOH SC-10A」導入事例
>富士フイルムテクノプロダクツ株式会社様
>株式会社小野測器様