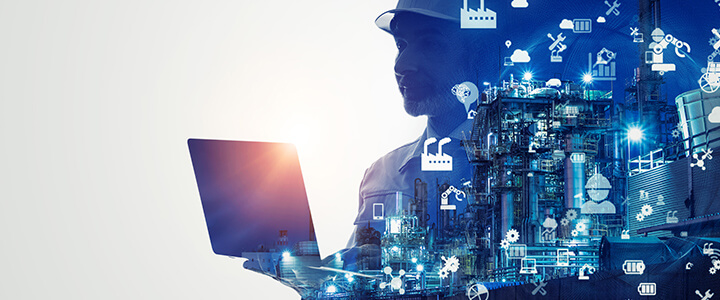
少子高齢化やグローバル化などにより、どの業界でもDXが急がれていますが、製造業においてもそれは例外ではありません。しかし、どのように進めれば良いのか、悩んでいる人もいるでしょう。
この記事では、製造業DXの事例をご紹介します。DXを推進するためのヒントを探していきましょう。
製造業におけるDXとは
そもそもDXとは、デジタル技術を活用して、業務をはじめ、さまざまなプロセスや組織、企業文化・風土までをも変革させ、効率化や利益の最大化を図ることです。
簡単に言うと、AIやIoTなどのデジタル技術を導入して、業務効率化・生産性の向上を目指そうということです。
製造業においては、製造工程にデジタル技術を用いることで、品質の向上や不良品率を低減しています。製品の品質を高めつつ業務の無駄を省くことで、従業員をはじめ、製品を利用した人々の生活をより良いものにすることを目的としています。
製造業におけるDXの重要性
日本では2022年に出生数が80万人を割り、今後もさらに少子高齢化が深刻化するのに伴い、生産年齢人口も減少していくことが予想されています。
また、製造業でのグローバル化が進むなか、世界市場の急速な変化に対応するには、需要の予測および業務の無駄を省く必要があります。
これらの課題を解決して、製造業として生き残っていくためにはDXが不可欠です。
DXを推進することで、製造過程におけるコスト削減、人手不足解消など、製造業におけるさまざまな課題の解決が見込めます。これにより企業活動の維持・発展に期待が持てるでしょう。
製造業DXの事例10選
ここでは具体的にどういった企業がDXでどのような効果を得ているのか、事例を見ていきましょう。
自社と似たようなビジネスモデルの企業の事例を知っておくことで、DXの足がかりを掴めます。
1. RFIDソリューション導入事例
プリンタシステムの製造を一手に担うシンフォニアテクノロジー株式会社の伊勢製作所では、プリンタの標準在庫部品の入出庫処理を手入力のバッチ処理で実施していましたが、複数の処理を一括で行うため、正確な在庫情報が把握できずにいました。これにより部品捜索に多大な時間がかかったり、部品の紛失トラブルが発生したりしており、ときに部品不足により生産が遅れることもあったそうです。
この課題に対して入出庫と在庫情報の見える化を図るため、RFID ソリューションを導入したところ、入荷部品の捜索時間が90%も削減。棚卸し業務時間も64%削減され、部品不足による生産計画遅延はゼロになりました。さらに現品票用紙代も年間5,000円削減されており、環境負荷の低減にも成功しています。
2. 沖電気工業株式会社 「バーチャル・ワンファクトリー」の取り組み事例
通信機器や現金自動預け払い機などの情報機器を提供する沖電気工業株式会社では、マスカスタマイゼーションへの対応や、社会変化による需要の減少といった危機感から、工場間の横串連携を検討。各工場で異なる製品を生産していましたが、共通する部品があるにも関わらず各工場で最適化した仕様設計をしていたために、共通の仕様での生産が難しい状況にありました。
そこで、対象となる2つの工場を仮想的に1つに融合する取り組みを開始。「部門間融合」「生産融合」「施策プロセス融合」「IT融合」を推進し、さらに各種設計情報の共通化にも取り組みました。
この結果、2工場における生産高は維持しながら効率化に成功しました。コスト削減はもちろん、2工場間の交流が活発化したことで技術の共通化や人手不足に応じた工場間の負荷分散など、外部環境の変化に対応できる生産体制の構築にも成功しています。
3. オークマ株式会社 「IT Plaza」の事例
オークマ株式会社では、主力商品であるNC工作機械の設計から生産までの全体最適を実現するため、下記の3軸を融合した生産システムモデルの「IT Plaza」を構築しました。
- ① エンジニアリングチェーンの連携
設計から製造までデータを一気通貫させて行うコンカレントエンジニアリングで開発リードタイムを短縮 - ② サプライチェーン連携
変動する生産計画への柔軟な対応のため生産管理情報をつなぎ、生産リードタイムを短縮 - ③ ナレッジマネジメント
日々の活動のなかで生まれる技術や技能を蓄積・共有
このシステムの構築にあたり、顧客や周辺機器メーカーなどをパートナー化。CRMやECM、SCMなどのツールの導入で連携を図り、共同でシステムやアプリケーション開発を行いました。その結果、トータルソリューションを創造する場の提供に成功しています。
4. トヨタ自動車株式会社 「工場IoT」の構築事例
製造やお客様から得たデータを技術開発に活かすことに苦戦していたトヨタ自動車株式会社では、効率や費用対効果の面から工場IoTに着手。3D CADデータなど既存のデジタル化データを一元管理化し、部署間にまたがる共有プラットフォームを構築しました。
構築目的の内の一つである「FA機器類からのデータ授受」の達成のために、ログデータとして現有資産に保管されたデータを有効活用。各事業部・工場で工場IoTのプラットフォームを使った現場プロジェクトを立ち上げ、取組の数を増やすことで総合的に費用対効果を上げています。
5. 三和工機株式会社「社内人材育成による設計力強化」の事例
三和工機株式会社では、特に設計・開発の請負事業において社内人材育成による設計力強化を実施しました。製造から設計側へのフィードバックの減少に伴い、エンジニアの設計力・エンジニアリング力が低下。一方で、顧客のメーカーでは、人材不足により即戦力が求められています。
これに対応するため、自社のエンジニア派遣事業と設計・開発の請負事業で蓄積したエンジニアリング上の業務への知見やノウハウを提供。さまざまなツールを使える人材を用意することで、企業や顧客のニーズを満たしています。
6. 株式会社アイデン 「IWS」の事例
主力事業の制御盤製造において、配線作業が職人の知見に依存していた株式会社アイデン。工程内での分業ができておらず、一人の作業者が終始生産にあたることも多々ありました。
作業においては経験・スキルが必要で、人材育成は時間がかかるため、作業の簡素化・単作業化を検討していたところで、CADベンダーとの連携を決意。工程ごとに必要な作業を標準化・可視化できるツール(IWS)を開発・導入しています。これにより、工程設計部分をあらかじめ設計・データ化することによりフロントローディングを実現しました。このほか、デジタル画面のデータを使用して一部作業の機械化を実施したことで生産性が向上するといった効果を上げています。
7. 株式会社IHI 「社内人材のデジタル人材としての育成」の事例
日々の生活を支える製品から航空や宇宙の領域に至るまで、多種多様な製品を製造している株式会社IHIでは、業務プロセスが部門ごとに個別最適化されていました。
これらのデータを効果的に繋げるために、高度情報マネジメント統括本部を設置。データの連携・活用において社外の専門家とも意思疎通ができるようにするため、自社製品や技術を知っている人材にデータの扱いを教えた方が良いという考えに至ります。
こうした背景によりデジタル変革に携わる人材を社内公募したり、事業部門を対象にデジタル人材育成プログラムを実施したりするなど、人材育成を開始。幅広いスキルや業務知識を有した人材が集まり、コーポレート部門単体で推進するよりも多様なアイディアが生まれやすくなった結果、より良い風土醸成に成功しています。
8. 株式会社ダイセル 「ダイセル式生産革新」の事例
株式会社ダイセルでは、各工場および各工場内の各工程で個別最適化がされており、グループ全体はもちろん、各工場全体での製造プロセス最適化ができていない状態でした。
そこで、オペレーションを「安全」「量」「品質」「コスト」の要素ごとに監視・判断・操作の流れで可視化。原理原則と照らしあわせて現場のノウハウを検証し、裏付けが取れたものをデータベースとして整理するなど、複数の取り組みを実施しました。
これにより製造プロセスにおける品質向上、安全性の強化、コスト削減、標準化を確立。「ダイセル式生産革新」として仕組み化に成功しています。他企業へのライセンス供与も行っているため、ダイセル式生産革新は広く普及しました。さらに、製造プロセスを確立したことで新規顧客の開拓にも繋がっています。
9. 三菱電機株式会社 「e-F@ctory」の事例
工場現場の自動化を図るFA機器を連携させ、工場内で眠っている価値あるデータを掘り出せば、コスト削減や品質向上に繋がると考えた三菱電機株式会社。ネットワーク技術の発展により、機器同士を接続できるインフラが整ってきたこともあり、工場内で生産情報とITを連携させる仕組み「e-F@ctory」の実現を試みました。
「e-F@ctory」では、工場設備IoTで製造現場起点の情報を取得し、エッジコンピューティングで処理することで、生産現場に近い場所でリアルタイムにデータを分析・活用できるようになります。また、クラウドシステムと連携することで、エンジニアリングチェーンとサプライチェーンを俯瞰した分析も可能です。ものづくり全体における生産性向上やコスト改善が目指せるようになりました。
10. ヤマハ発動機株式会社 「経営目線のデジタル改革実行」の取り組みに関する事例
ヤマハ発動機株式会社では、売上の最大化を最終ゴールに掲げ、デジタル改革を実行しました。
これまでも売上の最大化を目指していましたが、経営者目線が抜けていることに気づきます。また、国内・海外の拠点で独自システムが作られるなど、個別最適化が進んでおり、非効率なやり方が展開されていました。
そこで合宿や1on1ミーティングを実施して、経営陣の意識改革を実施。「既存ビジネスの効率化」と「未来のビジネスの創出」を目的に「デジタル戦略部」を立ち上げました。生産データの収集・分析、ナレッジのデータ化などを行い、さらには外部パートナーと連携して収集したデータの活用方法を検討しました。エンジニアリングチェーンの省人化・効率化の実施および新設組織でデジタル技術を使い、年間数十個のPoCを実施して不良品率を低減するなどの効果を上げています。
製造業でDXによって得られるメリット
製造業がDXを進めると、次のようなメリットを得られます。
● ダイナミックケイパビリティの導入
● 人材不足の解消
● 業務効率化・生産性の向上
● コスト削減
ダイナミックケイパビリティの導入
ダイナミックケイパビリティとは、企業が保有する資源を有効活用しながら、外部環境の変化に応じて自己変革を起こし、競合他社への優位性を保つことをいいます。変化が激しく不確実性の高い現代を生き抜くには、ダイナミックケイパビリティは必要不可欠になりつつあります。
このことにDXがどう関係しているのかというと、たとえばAIの導入により、急激な需要の変動が予測可能になります。さらに企業間でデータの連携を行えば、この変動にも耐えうる柔軟性の高いサプライチェーンの構築が可能です。
このように、DXを進めることで、保有資源を最大限に活かしつつ状況にうまく対応した企業活動が可能になり、企業のダイナミックケイパビリティを高められます。
業務効率化・生産性の向上
デジタル技術を活用すると、サプライチェーンの見える化が可能です。
各工程における無駄を洗い出しやすくなるため、業務効率化を進めることができ、人材の過剰配置を防げます。
さらにAIを活用して需要予測をすれば、閑散期に無駄に人員を投入することも、逆に繁忙期に人員不足を招くこともありません。
また、繰り返しの多い定型業務などは人ではなく機械に任せるようにすると、業務効率化はもちろん、ヒューマンエラーが低減されます。製造工程におけるトラブルも減少するため、生産性の向上が期待できます。
人材不足の解消
デジタル技術によりさまざまな業務の無駄を省くことができれば、作業工数も大幅に減ります。作業工数が大幅に減れば、必要な人員が従来よりも削減でき、人材不足の解消に繋がります。
また、人材育成においてもシステムを導入して、属人化している技術をマニュアル化できれば、技術の標準化が図れます。誰もが一定の基準で業務に当たれる状況を作っておけば、特定の業務における人材不足を感じることもなくなるでしょう。
コスト削減
前述していますがDXを推進すると、各工程の無駄を洗い出しやすくなります。
たとえば守衛所の無人化や製造工程における確認作業の自動化など、業務の簡略化や省人化が進めば人件費や生産コストが低減します。
まとめ
少子高齢化やグローバル化など、製造業を取り巻く環境によって引き起こされる課題は待ったなしで深刻化していきます。DXはこれらの課題を解決してくれる唯一の策といっても過言ではありません。業務の効率化を図り、生産性を上げて企業活動を継続・発展させていくためにも、できるところからデジタルツールの導入をはじめていきましょう。