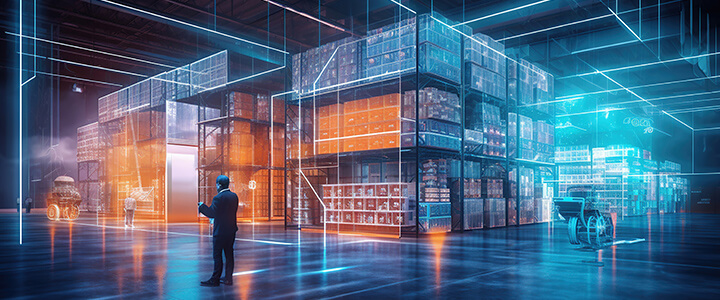
言うまでもなく、生産現場での安全性確保は最優先事項です。これは海外メーカーにおいても同様のため、世界的にも安全性の確保は重要な課題となっています。そのためこれまでさまざまな安全性対策が実践されてきましたが、通常の組み立てや製造ライン以外でも、「工場内物流」という視点で安全性の向上を図ることが可能です。
本稿では、「工場内物流の自動化」というキーワードで、どのような安全性対策が可能なのかを解説します。生産現場の安全性向上や工場内物流における安全対策などに課題をお持ちのご担当者様は、ぜひ参考にしてください。
生産現場での安全性の重要性
工場内の安全性の確保は大変重要であり、従業員の健康や生産性にも直結しています。
工場内での事故が発生すると、労働者の負傷や死亡、機械や設備の損傷など、労働者の生命に関わることに加え、企業の評判や信頼性にも大きな影響を与えます。
そのため安全性を向上させることは、事故のリスクを減らし、労働者のモチベーションや生産性を高めることになり、結果的に企業の生産性向上、コスト削減にもつながります。
工場内の安全性確保は、単なる法的義務ではなく、従業員が継続的に働く環境を整えられ、それが企業の持続可能性と競争力にも直結し、企業の信頼性と評価を高めることになります。
工場内で発生する事故の種類やその原因
製造現場における事故の種類
製造現場ではさまざまな道具を使い、多くの装置が稼働しています。また、場合によっては高所や危険物の近くで作業しなければならない場合もあるでしょう。安全性は製造現場において最も重要な管理指標の1つですが、それは、それだけ事故などの発生のリスクや影響度が高いためだからとも言えます。事故の発生は、作業員を危険にさらすだけではなく、ライン停止などによって生産工程全体に悪影響を及ぼします。工場内で発生する事故には、主に次のようなものがあります。
・はさまれ、巻き込まれ
製造現場で最も多い事故の1つが、「はさまれ・巻き込まれ」事故です。はさまれ・巻き込まれは、機械や装置の可動部分に身体の一部がはさまれたり巻き込まれたりして発生する事故。状況によっては重症や死亡する例も発生しています。機械の管理不良や操作ミス、操作スキル不足などが原因で発生します。
・転倒
「転倒」事故も多く発生しています。滑りやすい場所で作業する場合や、足元にある突起物や段差などにつまずいて転倒が発生します。物や機械が多い工場で特に発生しやすく、近くに危険物があったり転倒した際の打ちどころが悪ければ大きなけがにつながります。
・墜落、転落
次に起こりやすいのが「墜落・転落」事故です。高所での作業やはしごや脚立、リフトなどを使った作業の際に発生します。これも、クレーンを使った作業時などの場合は死亡などが発生する恐れがあります。
その他、機械や道具に接触して発生する「切れ・こすれ」や、空中から飛来したものに当たってけがをする「飛来物・落下物」による事故などがあります。
事故の原因
生産現場で発生する事故の原因には、大きく分けて人的要因として作業員の「不安全な行動」と、物的要因として機械などの「不安全な状態」があります。不安全な行動とは、安全な作業のために本来行わなければならない作業を怠ったり誤った方法で行うこと。例えば防護装置や安全装置などを無効にする、危険な状態を放置する、装置などを誤った方法で使用する、装置などのメンテナンスを怠る、適正な保護具(例えば自分のサイズにあったヘルメット等)や服装を装備・装着していない、不用意に危険な場所へ接近するなどがあります。
機械などの不安全な状態には、装置そのものの欠陥や防護装置や防護具の欠陥、部品の規格違い、物の置き方や作業箇所の不備、そもそも定められた作業手順自体に不備がある場合などがあります。
製造現場の安全性向上に対する取り組み
製造現場の安全性向上に関しては、従来からさまざまな取り組みがなされてきました。その代表的な例をご紹介しましょう。
5S
5Sは、「整理」「整頓」「清掃」「清潔」「しつけ」の各ローマ字の頭文字「S」を表したもので、より安全で効率の良い職場環境を実現するためのスローガンです。(※英語に直してもSort、Set、Shine、Standardize 、Sustainの5Sとなる)
必要なものと不要なものをしっかりと区別した上で「整理」し、どこに何があるのかが誰にでもわかる状態で道具や資材などを「整頓」しておくことで、物につまずいて転倒したり、危険な道具に触れてけがをしたりする危険性が減ります。
また、ゴミやほこりなどを取り除くだけではなく、機械や道具などをしっかりと「清掃」しておくことで、それらを安全かつ正確に使用でき、事故発生のリスクを抑えることができます。また、昨今ではウイルスや感染症の対策なども重要になってきています。
これらの整理・整頓・清掃された「清潔」な状態を維持することで継続的な安全性を確保することが可能になります。最後の「しつけ」は、清潔を保つためのルール作りと、それを習慣づけるための訓練を表します。決して強制的にではなく、従業員全員が5Sのためのルールを自主的に守ることができるようになれば、安全性が飛躍的に向上します。
KYT
KYTは、危険(Kiken)、予知(Yochi)、トレーニング(Training)の頭文字を表しており、作業員自らが現場に潜む危険に対してより高い感受性を持ち、それを解決するための能力を高めることを目的とした安全性向上のための訓練を指します。
「現状の危険を把握する」「重要度を分類する」「対策案を出す」「共通ルールと目標を設定する」の4つの段階があり、最終的な共通ルールや目標を掲示板に掲出したり唱和したりすることで実践に活かします。また、現状分析から対策までを各作業員自らが考えることで、危険予知や回避方法などを主体的に考えて行動する能力が養われます。
ヒヤリハット活動
「ヒヤリハット」とは、ヒヤリとしたりハッとしたりした出来事を表す造語で、ひとつ間違えれば事故につながったかもしれないような事象のことです。1931年、アメリカのハインリッヒ氏が行った調査によると、1件の重大事故の背景には29件の軽い事故、さらに300件のヒヤリハットが存在するというものでした。ヒヤリハット活動では、上記の調査結果に基づきヒヤリハットが発生した時点で原因を究明し対策を講じることで、大きな事故を未然に防ぐ活動です。ヒヤリハット活動では、発生した事象や原因、そして対策などを全作業員に周知し共有することが重要です。
AGVの機能と導入効果
資材や製品などの受け入れや出荷、また工場内で資材等を必要な場所に搬送する工場内物流の作業では、人による荷物の積み下ろし作業や移動・搬送中に、荷物の落下や転倒などの思わぬ事故が発生する恐れがあります。そのような作業を自動化・無人化することで、搬送時の事故発生のリスクを抑えることができ、作業員の負荷を軽減することもできます。
工場内物流を自動化する方法の1つが、AGV(無人搬送車)の導入です。AGVは、床などにテープで貼って走行ルートを設定し、そのルート上を自動走行する搬送ロボット。製造現場をはじめ物流拠点などで導入が進んでいます。台車型や低床型、牽引型などのさまざまなタイプがあり、現場の状況に応じて選択・適用が可能。工場内では、資材や製品の入出荷や、工場内での搬送に適用することで、搬送作業を自動化・無人化できます。
AGVによる搬送作業の自動化・無人化によって、工場内物流における事故発生リスクが低減。同時に重量のある荷物の積み下ろしなどの重労働から解放されることで作業負荷も軽減されます。AGVにはその他にも、正確かつスピーディーな処理が可能なロボットの強みを活かして搬送作業を効率化したり、無人化・省人化によって人件費を削減したりできるメリットがあります。
【関連コラム】AGV(無人搬送車)とは - 導入メリットや基礎知識
【関連事例】構内物流の省人化 ~無人搬送車(AGV)を活用して構内物流を効率化~
生産現場の安全性向上にも貢献するリコーAGV
リコーのAGVは、高精度ガイド方式を採用した光学式AGVです。一般的なビニールテープを床面に貼るだけで走行ルートを設定できるので、低コストかつ手軽に工場内物流を自動化。荷物の積み下ろしや搬送中の事故を防ぎ、工場内の安全性向上を図ることができます。コンパクト設計でしかも90度/180度ターンに対応するため、狭い場所でも稼働。狭くて危険な場所での搬送作業にも対応します。さまざまなシステム連携によって、工程の進捗状況に合わせた自動搬送にも対応。より広範囲の工程の無人化を実現することも可能です。リコーのAGVを導入することで、高い生産性と高度な安全性の双方を両立させることができます。
リコーAGV(無人搬送車)の詳細は下記からぜひご確認ください。
≫ AGV(無人搬送車) | リコー
セミナー紹介:AGV(無人搬送車)を活用した構内物流改革 ~リコーグループの構内物流効率化活動のご紹介~