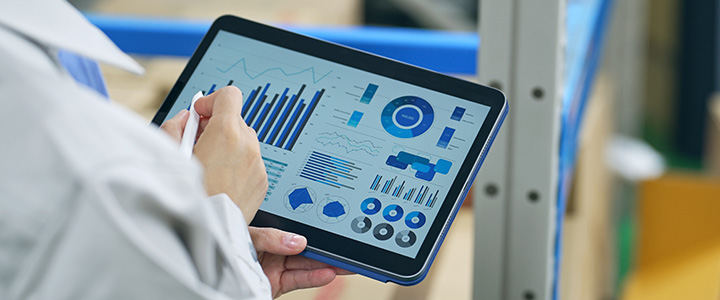
日本企業のDX化が急務とされ、DXを推進しないと経済損失が増大するとされる「2025年の崖」も近づきつつあります。日本企業の約10%を占める製造業にもDXの推進が求められています。
この記事では、製造業のDX推進の重要性と問題点、導入のメリットと進め方、ツール導入の実例について解説します。製造業でのDX推進を検討中の企業のご担当者様はぜひお読みください。
目次
DXとは
「DX(ディーエックス)」とは、デジタル技術を企業さらには社会に浸透させて、人々の生活をより良いものへと変革することです。
英語の「デジタルトランスフォーメーション(Digital Transformation)」を省略した語で、「トランスフォーメーション」は「変化、変形、変革」を意味します。「Trans-」で始まる語は「X」と省略されることが多く、「DT」ではなく「DX」と表記されます。なお「高級」の意味ではないので、読み方は「デラックス」ではありません。
企業においては、業務の改善にとどまらず、新しいビジネスモデルの創出など革新的な変化を起こすことをいいます。 単なるデジタル化ではなく、変革することを含むのが特徴です。
DXはさまざまに定義されますが、過去の技術で作られた「レガシーシステム」からの脱却や、新しいビジネスモデルの創出などを含むことも多くあります。
製造業におけるDXとは
製造業においては、DXとは「デジタル技術によって、品質向上や不良品の削減を目指すこと」であるといえます。それによって、人々の生活をより良いものにしていくということです。
細かい改善の積み重ねだけではなく、大きな変革が必要になることもあります。
新たなビジネスチャンスをつかむためにも、DXの導入・推進によって、臨機応変に対応できる力を高めておくことが大切です。
≫ 関連コラム:製造業におけるDXとは- DX推進の課題や成功のポイントとは
製造業におけるDXの重要性
製造業が抱える問題を解決するためには、DXが非常に重要だと考えられます。
まず、少子高齢化による人手不足が製造業の問題として挙げられます。
とくに中小企業の製造業の人手不足は慢性的かつ深刻となっています。人を増やすことができないなら、少ない人数で大きな成果を上げなくてはなりません。つまり、生産性を向上させる必要があるということです。
また製造業のグローバル化も製造業を取り巻く環境の1つです。グローバル化によって海外のメーカーとの競争にさらされるなかで自社が勝ち残っていくためには、企業価値や競争力の向上が重要となります。
DXの推進は、人手不足の改善や製造コストの削減につながります。製造業の維持と発展を促すことを期待されているのです。
製造業においてDXを図る際の3つの問題点
製造業においてDXを図る際には、以下のような問題点があります。
●社内にDXを任せられる人材がいない
●高いコストによってDXを図るのが難しい
●職人技術をデジタル技術によって補うのは難しい
それぞれについて解説していきます。
社内にDXを任せられる人材がいない
まず、社内にDXを任せられる人材がいないという問題が挙げられます。
日本ではデジタル人材がIT業界に集中しており、製造業には少ない傾向があります。社内に任せられる人材がいないと、そもそもDXに着手すらできないということになりかねません。
もちろん外注や委託はできますが、自社にノウハウを蓄積することが難しくなってしまいます。属人的な業務を排除できるのもDXのメリットや目的の1つですが、外注に頼りすぎると社内での共有や標準化ができません。やはり自社に対応できる人材がいないことは問題と言わざるを得ません。
高いコストによってDXを図るのが難しい
製造業ではDXのコストが高くなりがちで、これもDXを進める上で障壁となっています。
製造業は工場など設備の規模が大きくなる傾向があり、DXに多くのコストが必要となります。さらには製造拠点ごとに導入が必要となるので、教育コストやランニングコスト含めて費用がかさみがちです。
そのため多くの企業では、DXのためのデジタル機器に先行投資するよりも、現状の延長にあるような設備投資に偏ってしまっています。コロナ禍による業績悪化がそれに拍車をかけている場合もあるかもしれません。
職人技術をデジタル技術によって補うのは難しい
とくに町工場などの場合、職人の技術をデジタル技術によって再現するのが難しいこともあります。
熟練工の作業は経験やノウハウが属人化されやすく、技術の継承も、時間をかけて身に付けていく傾向があります。そのため作業内容がデータ化・デジタル化しにくいという側面があり、デジタル化しても再現性が低くなってしまうのです。
そうなると、職人技術をデジタル技術で補ったとしても効率が低下する可能性もあります。
製造業でDXによって得られるメリット
次に、製造業でDXを推進した場合に得られるメリットについてまとめます。具体的には次の4点が挙げられます。
●ダイナミックケイパビリティの導入
●人材不足の解消
●業務効率化・生産性の向上
●コスト削減
1つずつ見ていきましょう。
ダイナミックケイパビリティの導入
まず、製造業DXの推進が「ダイナミックケイパビリティ」につながることが挙げられます。
「ダイナミックケイパビリティ」とは、市場や顧客のニーズなどの変化に対応して自己変革していく能力のことです。
ダイナミックケイパビリティの3要素「感知」「捕捉」「変容」のすべてに、DXが役立つとされています。
●感知…環境の変化を敏感かつ的確に察知・把握すること
●捕捉…感知したビジネスチャンスを収益につなげる事業にすること
●変容…リソースを再編成しながら競争力を維持し続けること
デジタル技術を通じたデータの収集・分析により、現状の把握や変化の兆しの感知が可能になります。
さらにDXは、捕捉のための技術改良にも有益です。
また業務のデジタル化とは継続的に変容していくことであり、組織の再編成そのものであるともいえます。
人材不足の解消
DXは製造業の人材不足を解消するために役立ちます。DXにより業務の効率化や自動化が可能となり、より少ない人数で業務を回すことができるようになるからです。
人手を増やせるわけではありませんが、人材不足をカバーできるということです。
なお将来的には、人手を増やすのに役立つ可能性もあります。
高齢者や女性はフルタイムの勤務が難しい場合もあり、これまでは労働力として企業が採用しきれていない部分もありました。しかしDXを活用することで、短時間あるいはフレキシブルな勤務でも成果が上げられるようになることが期待されています。DXによってこれまで活用しきれていなかった人材を活用できるようになり、人材を増やすことにつながるのです。
業務効率化・生産性の向上
DXは、業務効率化・生産性向上につながります。
単純作業などは機械化に適しており、そういった作業にDXを活用すれば人間はより創造的な作業やコア作業に集中することが可能です。その結果、業務の効率化や生産性の向上がもたらされます。
機械はミスもしないため、作業の精度も高く保たれます。検査の時間も短くて済むほか、トラブルへの対処に時間を取られることも減るでしょう。その点でも、効率化や生産性向上が期待できます。
コスト削減
製造業DXはコスト削減にも役立ちます。
DXの導入により生産性が向上するのはすでに述べた通りです。生産性の向上とは、少ないリソースでより大きな成果を上げられるようになることです。ここでいう「リソース」には、労働時間や人手などが該当します。
これらのようなリソースが少なくて済むようになるということは、残業代などリソースに必要なコストを削減できるということです。
そのほか、労働時間の短縮によって機械や設備の稼働時間が短くなれば、それに伴って電気代や水道代なども節約できるようになります。
製造業DXの進め方
次に、製造業DXの進め方を解説します。
【製造業DXの進め方】
1.現場の状況を正しく把握
2.解決すべき課題の明確化
3.導入するシステムを決めて必要な情報を収集
4.システムを導入して社内環境に順応させる
5.業務プロセスの変更を試みてビジネスモデルの変革
それぞれのステップについて解説します。
1:現場の状況を正しく把握
まず初めに、現場の状況を正しく把握します。自社を観察し、問題点を客観的に理解することが重要です。
問題点や改善点があいまいなままでは、的確な施策がとれず成果を高めることができません。現状を客観的に把握することが改善の第一歩となります。
現状把握は現在の現場の作業を批判するためではなく、あくまで仕組みを改善することが目的です。
まず推進を取り仕切る側がそれを理解しておかなくてはなりません。そして現場にも理解を求めて、ありのままを見せてもらうよう協力を仰ぎましょう。もちろん現場の要望も丁寧にヒアリングしなくてはなりません。
2:解決すべき課題の明確化
次に、現状の理解で得られた課題点に優先順位を付けながら、解決すべき課題を計画化していきます。
各部署からの要望はそれぞれ切実かもしれませんが、全社的な視点で優先順位を考えましょう。
優先順位を決める際は、会社の一連の作業のうち上流に当たる部分を優先することが成功への近道です。
上流に当たる部分は範囲も狭く手を付けやすいこと、下流にも影響するため少ない労力で効果が見込めることが理由です。上流が整うだけで、下流までおのずと改善されることもあります。
そのほか中長期計画をDXの計画に反映させたり、逆にDXを導入することで中長期的にどのような方針で企業活動を行うのか決めたりすることも必要です。
3:導入するシステムやスマートデバイスを決めて必要な情報を収集
解決すべき課題と優先順位が明確になったら、どのような形で解決していくかについて具体的な方法を検討します。
課題解決に必要なシステムやスマートデバイスを比較・決定して、そのシステムを運用していくうえで必要となる情報を収集していきます。
DXは長期的・継続的に取り組むべきものです。定着させるためには、システムやスマートデバイスの使いやすさは大きなポイントとなります。運用を開始する前に教育を行うにしても、実際にシステムを使う担当者の全員がデジタル機器を使い慣れているとは限らないからです。
使いやすさ・見やすさなどと機能のバランスを考慮しましょう。
4:システムやスマートデバイスを導入して社内環境に順応させる
使用するシステムやスマートデバイスを決めたら、実際にシステムやスマートデバイスを導入して運用を開始します。
導入後は、社内の環境に合ったシステムになるようお互いの整合性を取ることが必要です。
システムの導入自体がDXの目的ではありません。目的はあくまで会社全体の効率化と変革です。そのためにはシステム導入をゴールとしてはいけません。
また全体の整合性を整えることなく一部の部署の都合を優先していては、会社全体が効率化されません。
5:業務プロセスの変更を試みてビジネスモデルの変革
運用を続けながら、ビジネスモデルの変革につなげるべく業務プロセスの変更を試みていきます。
DXの最終目的は「人々の生活をより良いものへと変革」することであり、ビジネスモデルの効率化と変革は自社にも社会にもプラスとなるからです。
トライアンドエラーを繰り返してPDCAを回しながら、少しずつ業務プロセスを改善していきます。そのためにはやはり継続が必要であり、継続していくためには使いやすいシステム選びが大切です。
製造業でのスマートデバイスの活用シーン
では、具体的に製造業でのスマートデバイスを活用するための目的を見ていきましょう。
部門ごとの活用による体制強化
スマートデバイスは導入する部門によって活用方法が異なります。例えば製造部門では、作業指示や品質管理に活用することで、作業の正確性と効率性を向上させることができます。一方、営業部門では、顧客管理システムを活用することで、営業活動の質を高めることが可能となります。
データ共有
スマートデバイスを活用することで、生産部門の各工程で得られたデータが共有でき、関係者が必要な情報にリアルタイムでアクセスできるようになります。また、データベースの一元管理ができることで、意思決定のスピードが向上し、生産効率も向上します。
各部門間の連携強化
スマートデバイスを導入することで、各部門間の連携がスムーズになり、製造現場からの情報をすぐに他部門と共有することができます。問題点の把握や、迅速な解決策の立案につながります。
開発体制の強化
スマートデバイスを活用することで、開発の効率化も図れます。デバイス上で設計図やマニュアルを閲覧することができ、開発作業者は手元に必要な情報を常に持ちながら作業できます。これにより、作業のミスを減らし、生産性を向上させることができます。
このように、スマートデバイスの活用は製造業の業務改善における最適な手段の一つとなります。
≫ 関連コラム:製造業の生産性向上に繋がるスマートデバイスの活用方法とは
製造業DXにおすすめのシステム
製造業DX向けのおすすめのシステムに、「リコーRFIDソリューション」があります。
リコーRFIDソリューションは、製造の進捗から在庫・物流・出庫にいたるまでのあらゆる管理の課題を解決できるサービスです。RFタグで情報を読み取ったり更新したりすることで、製造にかかわる業務の効率化を測ることができます。
部品在庫の適正化、製造の進捗と実績の見える化、資産や備品のロケーション管理、レイアウトの適正化などに役立ちます。プラットフォーム・サポート・タグなどのサービスや製品をご用意。すでに多くの製造業の企業様に導入していただいています。詳細はこちらからご確認ください。
以下に、実際に導入していただいた事例についてご紹介いたします。
「リコーRFIDソリューション」の導入事例①
まず、山梨県の中央電子株式会社 山梨明野事業所様(以下、中央電子)の事例です。
中央電子様は、幅広い産業分野に向けて、デジタル技術・ブロードバンド・IP技術などを駆使した最先端の製品開発を行っている研究開発型メーカーです。多品種少量生産による生産の複雑化という課題をお持ちでした。
リコーRFIDソリューションの導入により、大きく3つの効果が得られたといいます。
●作業実績データがリアルタイムに、正確に取得できるようになった
●可視化モニターによって、情報の共有化が図れるようになった
●ロスタイムも見える化できるので、迅速なフォローが可能となった
その結果、ボトルネック作業の正確な把握・レイアウト変更への活用などが可能となり、工場の生産能力向上が実現できました。
「リコーRFIDソリューション」の導入事例②
次に、三重県のシンフォニアテクノロジー株式会社 伊勢製作所様(以下、シンフォニアテクノロジー)の事例のご紹介です。
シンフォニアテクノロジー様では、プリンタシステムを生産しています。標準在庫部品の正確な在庫数量が把握できないという問題がありました。さらに部品在庫がわからないために、部品不足で生産が遅れるなど生産と管理の面で問題が発生していたといいます。
リコーRFIDソリューションの導入により、入出庫処理の自動化を実現するとともに適正な部品在庫の管理が可能になりました。部品在庫の可視化と適正管理が可能となり、入荷部品の捜索時間は90%削減。棚卸し業務時間も 64%削減されました。さらに部品不足による生産計画遅延もゼロを実現。QCDEすべてにおいて改善することができました。
まとめ
DXは、製造業の企業の存続に大きく寄与するものです。
製造業でのDX推進は難しい面もありますが、導入・推進することによって多くのメリットが得られます。むしろ将来的には、DXを進めないことによるデメリットが大きくなっていくことでしょう。「2025年の崖」を避けるためにも、積極的に導入を進めていくことをおすすめします。
DX導入を成功させるためには、継続しやすいツールの選定がカギとなります。ツールの選定でお悩みなら、まずはぜひリコーRFIDソリューションをチェックしてみてください。ご不明の点などありましたらお気軽にご相談ください。