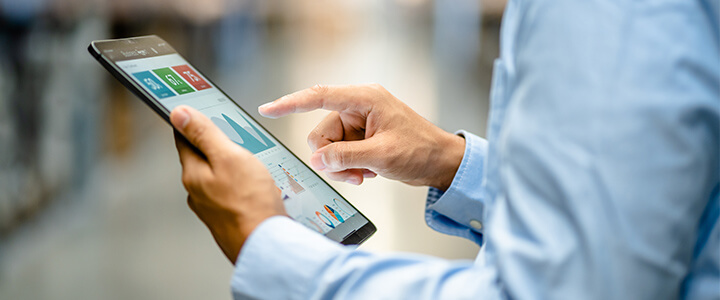
製造業でこれからDXを進める企業においては、過去に蓄積したデータをどう活用すれば良いか分からない場合もあるのではないでしょうか。
そこで今回は、製造業のDX推進におけるデータの重要性と活用方法をご紹介します。すでにDXを進めている企業のデータ活用事例も記載しているので、データ活用の参考にしてください。
製造業におけるデータの重要性
これまで、製造業におけるデータは「品質やトレーサビリティの担保」や「現場の管理」などで重要な役割を担ってきました。
しかし、昨今ではAIやIoTなど、さまざまなデジタル技術が台頭。企業間競争が熾烈化するなか、これらの技術を活用するのに欠かせないデータの重要性がさらに増しています。
また、労働人口の減少をきっかけに働き方改革が推進されていることも、データの重要性が高まっている理由として挙げられます。デジタル技術によってビッグデータを活用すれば、生産プロセス全体における無駄を洗い出しやすくなり、限られた労働時間・人数でも生産性を高めることができます。
データ活用が製造業にもたらすメリット
データ活用は製造業において、効率化や品質向上のキーとなります。特に、リアルタイムでの機械や部品の状態監視により、問題の早期発見と迅速な対応が可能になり、生産ラインの停止リスクを大幅に減少させます。このプロセスは、特定の部門に限らず、会社全体の生産性向上に寄与します。
また、データドリブンな判断に基づいた新たな製品開発やサービス提供は、顧客満足度の向上につながり、競争力の強化にも繋がります。さらに、大きなコスト削減にも寄与し、経営の最適化に貢献することが期待されます。今後、多くの製造業者がこのデータ活用の波に乗り、その効果を実際に確認し、採用していくことでしょう。
製造業におけるデータ活用の進め方
まず現場からのデータ収集とその解析から始めます。特に生産ラインの温度監視や機械の稼働状態など、リアルタイムでのデータ取得が重要です。これにより、特定の問題を発見し、早期に対処することが可能になります。
次に、これらのデータを統合し、全社的な視点から解析を行います。このプロセスにより、生産効率の向上やコスト削減、さらには新たなビジネスチャンスの発見につながる可能性があります。重要なのは、データを活用した判断を行い、事業運営に反映させることです。
多くのメーカーが、このようなデータドリブンなアプローチを進めており、今後もその傾向は加速することが期待されます。
製造業におけるデータの活用方法
製造業におけるデータの活用方法は次のようなものがあります。
● データを基に客観的な視点で意思決定
● より正確な製造計画の設定
● 品質の改善
● 人材不足の解消
● 効率化ツールへの活用
● 既存技術の可視化
これからの時代で特におさえておきたいのが、効率化ツールへの活用です。
労働人口の減少に加えて、DXの遅れによる経済損失が心配される2025年の崖が迫りつつある今、限られた人数で生産性をキープするには、効率化ツールの活用が必要不可欠です。
むしろ効率化ツールを活用することで、今よりも生産性を高められる可能性もあります。
データを基に客観的な視点で意思決定
製造業では、ベテランの勘や経験を元にした意思決定をすることがしばしばあります。そうした決定もときには大切ですが、頼りきってしまうと、ベテランの人たちが休みのときや退職した際、業務に支障が出るでしょう。
しかし、過去のデータから該当業務の傾向を分析できれば、曖昧性の高い経験則ではなく、確率に沿った意思決定が可能です。また、属人化の解消にもつながります。
より正確な製造計画の設定
在庫の回転率や納品までのリードタイムなど、過去のデータを参考に製造計画を立てれば、より正確な製造日程・納品日を算出できます。
精度の高い製造計画が立てられるため、納品予定日を大きく外れることも少なくなります。
納期遅れなどの可能性を減らすことができれば、取引先からの信頼を得やすくなるでしょう。
品質の改善
過去のデータを用いれば、製造過程において「どこで」「なにが」原因で不良品が発生しているのか傾向を掴めます。
傾向が分かれば、事前に対策を取ることも可能です。品質改善により、歩留まり率の向上が見込めます。
人材不足の解消
これまでに収集したデータを分析することで、業務プロセスにおける無駄を削減できるようになります。
作業工数を減らすことで業務効率化が実現できれば、人材不足を解消できる可能性があります。
効率化ツールへの活用
蓄積したデータを業務効率化ツールにまとめれば、平均値や合計値を分析できるため、需要予測や生産数、納期など生産計画の立案が容易になります。
これにより必要な作業人数や稼働時間、材料、資材なども、無駄なく準備できるようになり、コスト削減にもつながります。
既存技術の可視化
作業実績や手順、条件などをデータ化して可視化すれば、後輩教育において効率よく技術を継承できる可能性が高まります。「見て覚える」という感覚的なものではなく、データに基づいた継承を行うことによって、技術を平準化することもできます。
製造業DXにおけるデータ活用事例
最後に製造業DXにおけるデータの活用事例を4つ紹介します。
事例 1
製造やお客様から得たデータを技術開発に活かすことに苦戦していたとある企業では、効率や費用対効果の面から工場IoTに着手。3D CADデータなど既存のデジタル化データを一元管理化し、部署間にまたがる共有プラットフォームを構築しました。
構築目的の内の一つである「FA機器類からのデータ授受」の達成のために、ログデータとして現有資産に保管されたデータを有効活用。各事業部・工場で工場IoTのプラットフォームを使った現場プロジェクトを立ち上げ、取組の数を増やすことで、トータルでの費用対効果を上げています。
事例 2
とある企業では、製造業のサプライチェーン上におけるさまざまなデータをエンジニアリングチェーンにフィードバックし、フロントローディングのサポートを行っています。
IoTの現場データやPLM(製品ライフサイクルマネジメント)の製品データと基幹システムの原価データなどを相互に連携。経営指標を生成することによりトップダウンの意思決定を強化し、さらに現場には活動指標を浸透させて、全体最適に結びつく改善や改革を促します。
また、想定販売量や利益、設備稼働率、設備の投資回収状況などをデータで可視化。製品ごとの投資回収進捗や見通しの管理が可能になり、早い段階での経営判断につなげられるようサポートしています。
事例 3
DXの一環としてペーパーレス化を図った場合、デジタル化したデータの活用が難しく、思うように改善ができないこともしばしばあります。
RICOHのらくらくKAIZENサービスでは、作業員が持つスマートデバイスで撮影するだけで、現場のデータを取得、蓄積、活用ができます。現場の課題や改善において投稿した文章はWebブラウザで閲覧可能。サイト上でダッシュボードの表示ができるため、すぐにデータの分析・可視化ができるようになり、従来よりも短時間かつ効率よく改善活動が行えるようになります。
事例 4
とある企業では、生産ロットや、経過日数、生産環境など、さまざまな要因によって製品品質が変わるため、生産条件を見極めるためにビーカーでの予備実験を実施していました。
年間224時間もの時間を予備実験に費やしていましたが、予備実験なしで最適な生産条件を決めるため生産プロセスAIを導入。過去に蓄積された生産データと製品品質データの関係性をAIに学習させることにより、最適な生産条件を予測させました。この結果、予備実験にかかっていた時間を年間0時間にすることに成功しています。
まとめ
すべての業界に言えることですが、残業が多いなどを理由に製造業では特に人手不足が深刻化しています。そうした課題を解決するためにもDXは必要不可欠であり、DXを進めるためには過去のデータの活用が重要になってきます。
しかし、データを活用するにはまず同じ様式にまとめるところからはじめなければいけません。ここで躓いていてはDXも進められないので、データの取得から効率化できるツールの導入も検討してみることをおすすめします。