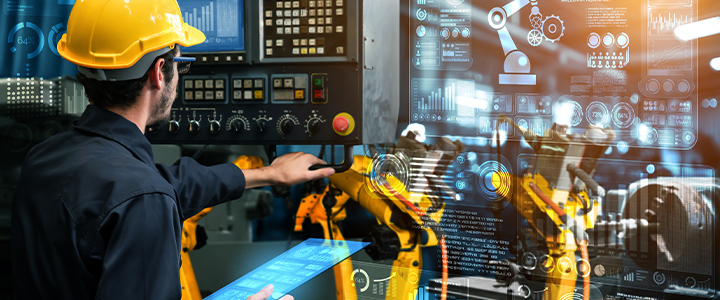
少子高齢化が進み、今後も国内における労働者人口の減少が見込まれることは周知のとおりです。これがさまざまな産業における事業構造に大きな変化をもたらす可能性があります。今後多くの企業が、人手不足や優秀な人材の確保、技術・ノウハウの継承、人件費高騰などの「人」にまつわる課題の解決を迫られることになります。これらの課題に対する有効な解決手段の1つが、製造業DXによる省人化です。
本コラムでは、省人化とはそもそもどういったものなのか、省人化を進める際のポイントなど、具体的な事例も交えて解説します。工場などの製造現場における人手不足などに課題をお持ちのご担当者はぜひ参考にしてください。
省人化とは?
省人化とはなにか
「省人化」とは、同じ製造工程や作業工程をより少ない作業員でまかなうことを言います。省人化の歴史は古く1950年代頃から主に鉄鋼業などを中心に意識されるようになりました。1960年代にはICが工作機械に組み込まれてさらに産業ロボットなどへ進展。自動車産業を中心に明確に省人化を目指した生産ラインが実現されていきます。
その後は、デジタル技術などの進歩によりロボットや工作機械がさらに高度化。近年はAIなどの最新技術の生産現場での実装も始まり、省人化をさらに推進する要因となっています。
省人化と省力化との違い
省人化を進める際に気を付けたいのが「省力化」との違いです。省力化とは各作業員の作業負荷を軽減すること。省力化による負担軽減によって、品質が向上したり安全性を高めたり、また、作業員の離職率を抑えたりする効果は上がるかもしれませんが、それだけではコスト削減などにはつながらない場合があります。
例えば10人で担当していた作業を5%省力化しても、作業負荷は減りますが作業員を減らすことはできません。省力化によって人件費を削減するには10%以上省力化して1人分の作業量を減らし、省人化にまでつなげることが必要です。
効率化や少人化という考え方も
似た言葉で「効率化」も頻繁に使われます。これはより広い視点で見た場合の生産性評価で、省人化や省力化もこの効率化の一種だと考えてよいでしょう。また、省人化をさらに発展させた「少人化」という考え方もあります。
少人化とは「その都度変化する生産数の増減に最適になるように作業員を動的に配置する」こと。これにより変動する生産需要に対応しながら、必要最低限の人的コストで生産ができるようになります。
工場に省人化が求められる理由
工場などの生産現場において省人化が求められる理由としては次のようなものが挙げられます。
人手不足の解消
周知のとおり製造業における人手不足は年々深刻になってきており、今後さらに加速していくことが予想されます。一般の作業員はもちろんですが、特に顕著なのが優秀な技術者の不足。優れた人材に負荷が集中することで人材の定着率が下がってしまう、という悪循環も生じています。省人化はこのような人材不足の問題を解消する手段として期待されています。
人件費の抑制
省人化は同じ製造工程をより少ない作業員でまかなうことですので、その分の人件費を抑制することができます。人件費を抑制することでコスト削減できれば製品のコスト競争力が向上し、余剰となった資金を新たな投資などへ回すことも可能になります。
生産性の向上
省人化のために新たな生産設備を導入することで、製造工程全体の生産性が向上します。さらに、一旦最新設備を投入するとその後も新たな人材を増やさずに設備投資のみで生産性向上を図ることも可能になり、中長期的な増産計画なども立てやすくなります。
働き方改革の推進
省人化による生産性向上が作業員にかかる作業負荷軽減につながります。また、自動化などが進むことで危険な作業や劣悪な環境下での作業が減少。加えて効率化によって時間外労働が減ったり 年次有給休暇や育児休暇などが取得しやすくなったりするなど、働き方改革を推進させます。
技術・技能承継問題の解消
人手不足に加えて製造業で課題となっているのが、技術・技能承継の問題です。高度な技能を有する熟練工の退職などに伴い、その技術・技能の継承ができないことが問題となっています。省人化の際の自動化や機械化によって対象の製造技術が標準化や可視化されることで熟練工への依存度が減少し、技術・技能継承の問題が生じにくくなります。
省人化の進め方と注意点
続いては、実際に省人化を進めていく際の手順と注意点について順を追ってご説明します。
既存業務の分析と見直し
まず行いたいのが、現在の業務や作業内容の分析と見直しです。無駄な業務や非効率な業務がないか、作業負担が大きな業務がないか、わざわざ人が行う必要のない作業はないか、など省人化の候補となる作業・業務の洗い出しを実施します。無駄な部分や非効率な部分は、省いたり効率を改善することで工数削減を図ります。作業負担が大きかったり人が行う必要がなかったりする部分に関しては、後述の自動化の対象候補となります。
作業の標準化・文書化
全体の作業分析が完了し、無駄等を省いた後に作業の標準化に着手します。作業担当者間での手順の違いを吸収して統一し、それをマニュアルとして文書化します。標準化と文書化によって、誰でも同様の効率で作業できるようになり、さまざまな作業に柔軟に従業員を割り当てできるようになります。もちろん品質の安定にも寄与します。
また、作業の標準化を確立し継続的な改善と定着を行うためには、生産現場における定期的な安全衛生巡視や工場内検査を実施し、そこで発覚した不備や課題を、スムーズに関係者へ共有・連携可能な仕組みと、是正・検証のサイクルを効率的に回すことが重要となります。これらを実現するために、スマートデバイスとクラウドサービスを活用した「生産現場のDX対応」が注目されています。
【製造現場の課題をらくらくKAIZEN】
≫ RICOH らくらくKAIZENサービス
生産ラインへの最新技術や設備導入による自動化・効率化
上記の分析で特に非効率な作業や、負担が大きかったり人が行う必要がなかったりする作業に関しては、ロボット等の最新技術や設備の導入による自動化や効率化を検討します。昨今製造業においてもAIやIoT、ビッグデータなどのデジタル技術を中心にしたさまざまな技術活用して、製造工程を効率化しようとする動きが活発になってきています。また、製造設備も高度化してきており、それらを活用・導入することで電子部品工場から大型機械工場まで様々な生産ラインの自動化などを実現する事例も増えてきています。
生産ラインの自動化は、現状の生産量を維持したまま生産ラインの省人化を行うためには、非常に有効な手段となります。例えば、中国では急速な少子高齢化による労働人口の減少に対応するため、全ての生産ラインが自動化されたスマート工場が増加しており、少ない人数で大量の商品を生産可能な体制の構築が進められています。
いきなりすべての生産ラインを自動化することは、ハードルが高いという企業も多いかと思いますので、まずは「時間のかかる人力の作業」「人力の作業によるミスが多い工程」を自動化することから検討していくのが良いでしょう。
このような自動化を実施するには、設備投資は必要となりますが、人件費や不良品を削減できるメリットを考慮すると、生産性向上のための一手として十分に検討する余地があります。
リコーの社内実践による工場の省人化事例
生産現場における省人化はさまざまな企業で取り組まれています。その代表的なものの1つが、多関節ロボットを導入した組み立てや検査工程の自動化です。無人搬送機(AGV)を工場内に導入し資材の搬送を省人化する企業も増えつつあります。また、近年AIを活用した機械学習や画像認識技術によって検査や品質管理を省人化する取り組みも盛んです。
無人搬送車(AGV)を活用し省人化を推進
リコーグループの工場にてAGVを活用した省人化事例をご紹介します。
● AGVとは
AGVとはAutomated Guided Vehicle の略称であり、床面のテープを認識しながら走行する無人搬送車です。主に工場/倉庫内で物品の搬送を行なう装置のことで、構内物流の無人化/省人化に貢献します。
リコーが開発したAGVは従来の磁気式ではなく、光学式のため、走路変更のコストも手間もかかりません。
● 導入した結果
当社リコーでは従来は、工場内のパーツ運搬はハンドリフトで行っていましたが、AGV導入後は運搬作業そのものが0となりました。作業者がピッキングした荷物を置くだけでAGVが自動運搬してくれ、レイアウト変更や業務の流れを大きく変えずに自動化をすることが出来きたため、人による運搬作業が不要となります。また、今までの生産現場では、作業者によるハンドリフトの運搬スキルにムラがあり、余裕をもった生産計画を立てていましたが、AGV導入後は、決められたルートを決められた速度で運搬するため、確実な生産計画を立てることが可能になりました。
詳細は以下リンク先でご紹介していますのでぜひご覧ください。
【実践事例】
≫ 製造ラインの省人化で生産性向上