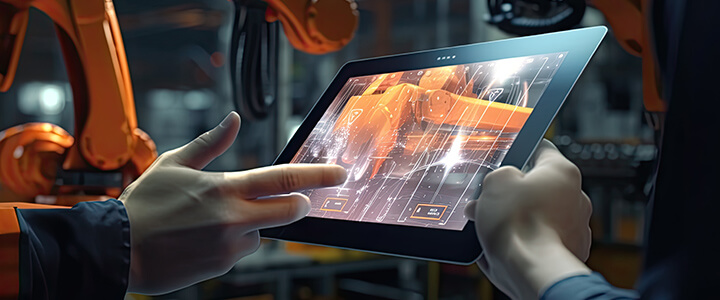
製品の品質や信頼性の維持・向上のためには、製造工程における検査は欠かせないものです。一口に検査と言っても、その方法や目的などによりさまざまな種類があります。その中でも、「外観検査」は多くの工程で採用されている重要な検査方法の1つ。
本稿では、さまざまな検査方法について確認した後、外観検査とはどういうものか、さらに外観検査の精度や効率を向上させる「画像検査」とはどういった検査方法なのかを解説します。外観検査に関わる担当者様はぜひ参考にしてください。
製造業における検査の目的と種類
検査の主な目的
初めに、製造業における検査の目的を確認しておきましょう。製品を製造する場合、仮に最新の製造装置を用いたり熟練工が担当したり、さらに細心の注意を払ったとしても不良品の発生を「ゼロ」にすることはできません。しかし、発生した不良品をそのまま放置すれば市場に出回ってしまい、自社の信頼が損なわれます。そのような事態を避けるのが検査の主な目的の1つです。
その他にも、製品の製造品質を向上させることも重要な目的です。検査によって、どの工程でどのような不良品が発生したのかを特定。その情報を製造工程にフィードバックすることで、製造品質を向上させることができ、不良品の発生を抑制できます。
製造工程別の検査の種類
それでは、製造工程別ではどのような検査があるのかを見てみましょう。
まず原材料や部品、半製品などの受け入れの際に、その適否を判定する「受入検査」があります。受入検査によって規格外の部品などが製造工程にわたるのを防ぐことができます。
工程間で、前工程で製造した半製品などを後工程に流してもよいかどうかを判断するのが「工程間検査」です。工程間で検査することで手戻りを最小限に留めると共に、不具合が発生している工程が特定できます。
完成した製品が最終的に規格や基準を満たしているかどうかを判定するのが「最終検査」です。これにより不良品が市場に出回るのを防ぐことができます。
その他の検査の種類
工程別の他にもさまざまな検査の種類があります。検査対象に与える影響によって、製品を破壊せずに目視や超音波などによって検査する「非破壊検査」と、引張試験など製品を破壊する「破壊検査」に分けることができます。
また、検査の方法により、ロット内全品を検査する「全数検査」や一定のサンプルのみを対象にする「抜取検査」、供給元が実施した検査内容を確認することで合否を判断する「間接検査」などがあります。
さらに品質の検査という観点では、キズや欠け、汚れ、異物混入、印刷ミスなど製品の外見上の欠陥を確認する「外観検査」と、仕様どおりに動作するかどうかを確認する「機能検査」があります。
検査方法を選択する際のポイント
検査方法などを検討する際には、次のような点を確認します。
まず、検査を実施することでどの程度損失を防ぐことができるのかを明確にします。検査なしで不良品が流通してしまう場合の損失と、検査を実施する際の費用を比較して、前者の方が大きいのであれば検査の費用対効果があるということになります。
また、破壊検査であれば抜き取りで、製品の安全性など重要度が高いものなら全数を対象にするなど、検査の内容や項目などによって最適な検査方法を判断します。
さらに、取引先から検査方法の指定や要望がないかどうかも事前に確認しておきます。
外観検査の内容・種類
外観検査とは
製造した製品の品質を確認する目的で実施される外観検査は、受入から工程間、最終検査まであらゆる工程で実施されています。外観検査の具体的な内容は製品によって異なりますが、通常は仕様書に基づいて決められます。
一般的には
「仕様や形状、構造の検査」
「製品表面形状の検査」
「仕上がりの検査」
の3つに分類されます。
仕様や形状、構造の検査
形状や構造、寸法、色、意匠・印刷が、製品の規格や仕様書で定められた基準から逸脱していないかどうかを検査します。変形や位置ずれ、寸法違い、変色、意匠や印刷などを確認します。
製品表面形状の検査
製品表面にキズやスレ、凸凹やムラ、そしてほこりや汚れなどの付着物がないかどうかを検査します。検査員や検査条件などによって結果がぶれやすいため、良否の判定が難しい検査だと言われています。基準書などをあらかじめ作成することで、検査結果のブレを抑えることができます。
仕上がりの検査
バリや突起、治具などの加工跡が残っていないかどうかを検査します。直接製品の機能には影響する項目ではありませんが、製品品質を高めるためには重要な検査です。
外観検査には、さらに目視検査と画像検査の2つの方法があります。
目視検査のメリットと課題
目視検査とは
目視検査は人間の五感(視覚・聴覚・味覚・嗅覚・触覚)を用いて行う官能検査の1つです。目視による外観検査では、人が実際に目で見て、前章で挙げたような製品の構造や表面形状、仕上がりなどを検査します。
効率性を重視して製造ライン上で実施するインライン検査と、検査精度を重視して製造ラインとは別の工程で実施するオフライン検査の2通りの方法があります。
目視検査におけるメリットと課題
目視検査のメリットは、検査機械などの導入・運用コストが掛からない点がまず挙げられます。検査する作業員のスキルや経験によっては、非常に精度の高い検査を実施できることもメリットです。
また、目視検査のような人が直接行う官能検査に対する信頼度は依然高く、取引先などへのアピールポイントにもなります。
反対に課題としては、検査する作業員の技能に結果が左右されやすく、誤差が生じやすいという点が挙げられます。
また、連続して検査を続けると作業員の負担が大きくなります。さらに、優秀な検査技能者を育てるためには、相当の時間とコストが必要になります。機械などを使った場合と比較して、必ずしも効率的に検査できないという点もデメリットと言えるでしょう。
画像検査のメリットと導入時のポイント
画像検査のメリットと課題
カメラで撮影した製品画像を基に、画像認識システムなどによって自動的に外観検査を実施する方法が画像検査です。画像検査のメリットは、まず検査の品質を均一化・標準化できること。前章で述べたとおり、目視検査では検査する作業員のスキルや集中力などによって、どうしても検査結果にバラつきが生じます。画像検査ではそのようなバラつきを抑えることができます。また、見えにくい箇所の不具合や微細なキズなど、目視では見つけにくい対象を発見できるのも画像検査の強みです。
検査する作業員が不要になるため教育コストが不要になり、かつ検査に従事していた人材リソースを他の業務に回すことができるというメリットもあります。その他、検査効率が向上したり、検査する作業員の負荷を軽減したりするなどの効果も期待できます。
一方画像検査においては、システム導入時に初期コストが必要になることや、検査のための良品の定義や各種設定などの準備作業が必要になることが課題です。
導入時のポイントと適用例
画像検査を導入する際には、まず自社の検査作業においてどのような課題があるのかを把握。さらに、実際の検査対象となるワークや検査項目などを分析し、その結果に基づいて画像検査のシステム化範囲や方式などを決定します。場合によっては他システムとの連携やセキュリティに関して検討する必要が生じるかもしれません。
画像検査は多くの工程に適用されていますが、具体的には次のような適用例があります。電子部品製造では非常に微細な欠陥が大きな影響を及ぼします。画像検査を用いることで、人間の目では到底見えないような極小の欠陥でも素早く発見することができます。
食品製造で取り扱う食品は、その形や色、サイズなどが品質を示す非常に重要な要素です。画像検査を活用すれば、それら複合的な要素を一度に検査することができます。
また、特に外観のバラつきが大きい生鮮食品などの場合は、AIを活用した検査も有効です。
製造業のヒューマンエラー対策に活用できるシステム
製造業のヒューマンエラーは、専用ツールを活用して確認作業を自動化することでも対策できます。
本章では、リコーの現場支援システムの中から、おすすめの製品を2つピックアップしました。
- ● RICOH SC-10A
- ● RICOH SC-20
それぞれの概要と一押しポイントを紹介します。
RICOH SC-10A
「RICOH SC-10A」は、現場における作業支援に特化した高倍率レンズ搭載のカメラシステムです。作業工程を画像でオート認識することで、目視による不注意や誤認を起こさせません。
チェックに必要な機能がオールインワンになっているシステムであり、セットアップも簡単です。リアルタイムでの情報共有が可能になり、ヒューマンエラー対策が手軽になります。
リコー「RICOH SC-10A」の詳細はこちら
作業支援カメラ RICOH SC-10A|リコー
RICOH SC-20
「RICOH SC-20」は、人の手による作業工程におけるミスを監視するカメラです。検査と同時に品質チェックもリアルタイムで行えることが特徴であり、確認に必要なすべての工程をオート化できます。
チェックポイントは20カ所まで設定でき、作業後の一括点検も可能です。低コストかつパソコン不要で導入できる手軽さから、幅広い現場に喜ばれています。
リコー「RICOH SC-20」の詳細はこちら
作業検査カメラ RICOH SC-20|リコー