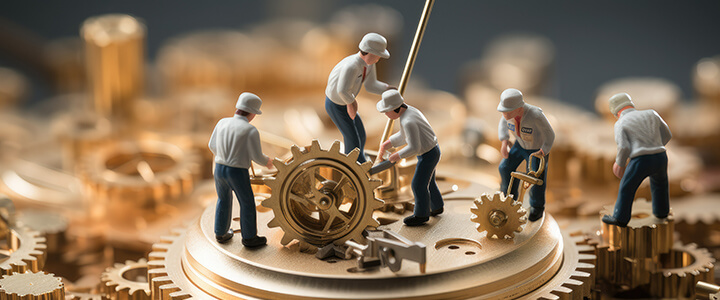
ヒューマンエラーは、業務を遂行する上での重大な障害となります。しかし、ヒューマンエラーという用語自体は知っていても、その種類や原因を構造的に理解している方は少ないのではないでしょうか。ミスやトラブルの発生後に対処するだけでは、いずれ取り返しのつかないような大問題に発展するかもしれません。
本記事では、ヒューマンエラーの概要と起こしやすい人の特徴をふまえ、発生要因と対策を解説します。ヒューマンエラー防止に有効なシステムもあわせて紹介しますので、どのような対策を講じるべきかお悩みの方はぜひ参考にしてください。
目次
ヒューマンエラーとは
ヒューマンエラーとは、簡単にいうと人為的なミスのことです。なお、システム不良や設備・機器の説明書の不備などではなく、あくまでも現場における作業者側の何らかの過失を原因として発生したトラブルをヒューマンエラーと捉えられています。ただし、上記のような不良・不備も、元をたどればヒューマンエラーに起因しているケースが大半です。
機械とは異なり、人間が一分の隙もなく正確に作業をこなすのは不可能なため、さまざまな原因によってヒューマンエラーが発生します。小さなミスでも、場合によっては社会的信用を大きく損ねる要因になるケースもあるため、あなどってはいけません。ヒューマンエラー防止のためには、あらかじめ起こりうるあらゆる人為的リスクを想定し、対策を講じておくことが重要です。
ヒューマンエラーの種類
ヒューマンエラーには、大きく分けて故意と過失の2種類があります。過失は意図的に起こるトラブルです。手抜きや横着なやり方によるものであり、作業者の意思が関わっています。
対して過失は、意図せずに起こるミスです。作業者がわざと起こしたわけではなくとも、誤認や不注意などによりヒューマンエラーは発生します。
それぞれの原因の詳細は下記の章で改めて言及しますので、そちらをご覧ください。
ヒューマンエラーが多い人の特徴
ヒューマンエラーが多い人の特徴は、以下のとおりです。
- ● 知識不足
- ● 慎重さに欠ける
- ● 他者とのコミュニケーションが不得意
- ● 受動的
- ● 客観視できない
- ● ストレス管理が苦手
第一に、業務に関する知識が足りないと正確な作業は困難でしょう。細部まで注意を向けない場合、思わぬ見落としがよく起こります。
また、独断で作業にあたるとミスが起こりがちのため、どのような現場であってもコミュニケーション力が必要です。常に受け身で指示待ちの姿勢だと、業務に対して主体性や責任感が薄く、ミスを起こしやすい傾向にあります。
同時に、自らを客観視できないと、体調不良や力不足による判断ミスに気付けません。ストレス過多の状態では苛立ちや不安感が強まり、普段は起こさないようなトラブルが起きる危険性が高まります。
上記の特徴に当てはまるからといって必ずしもヒューマンエラーを起こすわけではありませんが、注意しておくに越したことはありません。
ヒューマンエラーが発生する5つの要因
SHELLモデルによると、ヒューマンエラーは以下5つの要因で構成されるといわれています。
要因 | 概要 |
---|---|
手順書やマニュアル・規則(Software) | 根本的なルールや従業員への教育システム |
設備や機械(Hardware) | 操作する設備や機械などのモノ |
作業環境(Environment) | 空調や照明、騒音対策のほか、現場の雰囲気なども含む外的環境 |
本人(Liveware) | 作業を行う当事者の身体的・精神的状態 |
周囲の人間(Liveware) | 作業の当事者と現場で関わるすべての人 |
なお、SHELLモデルとは、ヒューマンエラーの要因を構造化したものです。KLMオランダ空港の機長だったフランク・H・ホーキンズ氏が提唱した説であり、上記要因の頭文字を由来として名付けられました。
SHELLモデルでは、ミスが起こることを前提とし、人的リソースがシステムの中心に位置付けられています。周囲に配置された上記5つの要因と関係性を照らし合わせることで、ヒューマンエラーがなぜ起こるのかを理解しようとする考え方です。
製造業で起こるヒューマンエラーの原因
ここからは、製造業でよく起こるヒューマンエラーを下記2つの項目に分け、その原因について考えていきましょう。
- ● 意図して起こるヒューマンエラーの原因
- ● 意図していないヒューマンエラーの原因
それぞれの原因の特徴を説明します。
意図して起こるヒューマンエラーの原因
意図して起こるヒューマンエラーの主な原因としては、横着してしまう、またリスクを過小評価してしまうことが考えられます。これらは作業者の過失による不注意が起因となり、ヒューマンエラーとして表面化したトラブルです。
それぞれの詳しい原因を見ていきましょう。
横着
意図的な行動によって引き起こされたヒューマンエラーの原因の代表例ともいえるのが、作業者の横着な態度・意識です。作業工程が少しでも楽になるよう手を抜くと、さまざまなトラブルが起きかねません。横着な心理によるヒューマンエラーは、ベテラン従業員による慢心のほか、作業に慣れ始めた頃にもよくみられるミスだといえます。
リスクの過小評価
リスクの過小評価とは、端的にいうと判断ミスです。チェックや報告・連絡・相談などの重要性を取るに足りないことだと捉え、怠った結果としてヒューマネラーが起きるケースは少なくありません。
意図していないヒューマンエラーの原因
意図していないヒューマンエラーの原因としては、以下9つの例があります。
- ● 物忘れ
- ● 確認不足
- ● 認識違い
- ● 疲労
- ● 作業負荷
- ● 思い込み
- ● 連携不足
- ● 作業環境の悪さ
- ● 作業者の知識・経験不足
各原因の理由と背景について考えていきましょう。
物忘れ
わざとではなくとも、重要な工程をついうっかり忘れてしまうことは誰にでもあることです。記憶とは薄れやすいものであり、きちんと覚えていると思っていても、ルールが視覚化されていないとすぐに忘れてしまいます。
確認不足
確認を怠り、重大なミスを見落としたり思い違いをしたりする事例が後を絶ちません。横着と原因が似ているものの、確認不足によるヒューマンエラーはわざとではないからこそ対策が難しい面があります。
認識違い
ルールや作業内容の認識を見誤ると、意図せずミスしてしまうでしょう。あいまいな指示を出すと、認識違いが起こりやすいため要注意です。
疲労
疲労が過度に溜まった状態だと、通常よりもパフォーマンスが低下します。眠気で体が思うように動かず、集中力や注意力も散漫になるでしょう。作業者本人が気付かぬ間に、疲労が蓄積されているケースもめずらしくありません。
作業負荷
作業内容や工程が煩雑すぎるあまり、作業員に過度な負担を強いている状況がヒューマンエラーを誘発しているケースもあります。また、大量かつ長時間におよぶ単純作業の連続も、注意力・集中力の低下を招きかねません。
思い込み
先入観や固定観念が強いと、思い込みによるミスが起こりやすいといえます。特に、通常とは異なる条件下ではヒューマンエラーが多発する傾向にあるため、注意しなければなりません。
連携不足
現場での連携が十分に取れていない場合、ヒューマンエラーの回避は困難です。情報共有体制の不備を解消しないことには、根本的な問題を解決できません。
作業環境の悪さ
現場の空調や照明が整備されていない場合や、設備のメンテナンス不足なども、ヒューマンエラーの一因です。作業環境が悪く、安全性が低い現場では、ミスやトラブルが起こるべくして起きたといっても過言ではありません。加えて、現場の雰囲気や社風などによる集団欠陥も作業環境を悪化させる要因になります。
作業者の知識・経験不足
現場に入って間もない新人は、業務に関する知識や経験が乏しく、教育が不十分だとヒューマンエラーを起こしがちです。他方で、ベテランでもルール改正や業務プロセスの変更に対応できておらず、知識が足りないケースはよくあります。また「経験があるのだからこれくらいできる」という思い上がりから、ヒューマンエラーが起こることもめずらしくありません。
製造業で起こるヒューマンエラーの防止策
製造業で起こるヒューマンエラーは、以下の対策を講じることで予防できます。
- ● 危険予知活動を行う
- ● コミュニケーションを活性化する
- ● 作業環境を整備する
- ● 教育を強化する
- ● 確認を習慣付ける
- ● マニュアルを作成する
各防止策のポイントや注意点を確認していきましょう。
危険予知活動を行う
あらかじめ起こりうるリスクを把握している場合としていないケースでは、ヒューマンエラーの発生頻度が大きく異なります。グループ討論やポスター・標識の掲示など、危険予知訓練(KYT)を日常的に行うことで、ヒューマンエラーを最小限に抑えられるでしょう。
コミュニケーションを活性化する
意図していないヒューマンエラーは、コミュニケーション不足から起因しているものも多いものです。したがって、コミュニケーションの活性化が作業環境の改善につながります。連絡系統の見直しに加え、相談しやすい雰囲気作りも大切です。
作業環境を整備する
作業に集中しやすい環境に整えれば、不注意によるヒューマンエラーが減らせるでしょう。劣悪な環境下での作業では、従業員の体調にも悪影響を及ぼしかねません。現場内のレイアウトを改善するほか、温度・騒音管理や安全対策を徹底してください。
教育を強化する
定期的な研修や勉強会を開催するなど、従業員への教育を強化することで、現場におけるリスクリテラシーを高められます。作業に当たる際の意識の持ち方や安全確認の重要性を再認識させ、ヒューマンエラーを防ぎましょう。ただし、プレッシャーを過度にかけるのは逆効果です。それぞれの特性に応じ、適した教育を施すことが重要です。
確認を習慣付ける
ヒューマンエラーを軽減するためには、チェック工程の見直しが欠かせません。従業員一人ひとりに点検を習慣づけるのはもちろん、チーム全体における確認体制を強化することで個人によるヒューマンエラーの発生を抑制できます。
マニュアルを作成する
わかりづらく煩雑な工程を全従業員に理解させるためには、マニュアルの作成が必須です。整備されたマニュアルがあれば、独断による判断ミスを回避できます。作成時には、現場の意見も取り入れつつ、誰にでもわかりやすいマニュアルになるよう配慮しましょう。
製造業のヒューマンエラー対策に活用できるシステム
製造業のヒューマンエラーは、専用ツールを活用して確認作業を自動化することでも対策できます。
本章では、リコーの現場支援システムの中から、おすすめの製品を2つピックアップしました。
- ● RICOH SC-10A
- ● RICOH SC-20
それぞれの概要と一押しポイントを紹介します。
RICOH SC-10A
「RICOH SC-10A」は、現場における作業支援に特化した高倍率レンズ搭載のカメラシステムです。作業工程を画像でオート認識することで、目視による不注意や誤認を起こさせません。
チェックに必要な機能がオールインワンになっているシステムであり、セットアップも簡単です。リアルタイムでの情報共有が可能になり、ヒューマンエラー対策が手軽になります。
リコー「RICOH SC-10A」の詳細はこちら
作業支援カメラ RICOH SC-10A|リコー
RICOH SC-20
「RICOH SC-20」は、人の手による作業工程におけるミスを監視するカメラです。検査と同時に品質チェックもリアルタイムで行えることが特徴であり、確認に必要なすべての工程をオート化できます。
チェックポイントは20カ所まで設定でき、作業後の一括点検も可能です。低コストかつパソコン不要で導入できる手軽さから、幅広い現場に喜ばれています。
リコー「RICOH SC-20」の詳細はこちら
作業検査カメラ RICOH SC-20|リコー
まとめ
作業に人の手が加わる以上、すべてのヒューマンエラーを完全になくすことはできません。しかし、人はミスを犯すものということを正しく認識し、工夫次第で発生頻度を最小限にすることは可能です。作業環境を整えて従業員へ適切な行動を促すとともに、対策ツールを効果的に取り入れることでヒューマンエラーを防止しましょう。
製造業の生産ラインにおけるヒューマンエラー対策にお困りの際は、ぜひリコーへご相談ください。おすすめの製品の紹介のほか、お見積もりや無料トライアルも実施しておりますので、この機会に検討してみてはいかがでしょうか。