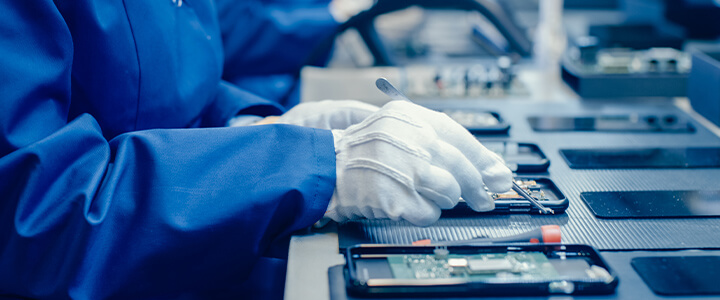
製造業においては、部品の組み付けや機械操作など、さまざまな作業において、ヒューマンエラーによる不良品の発生や事故の発生が課題となっています。これらの課題を解決するために、ポカヨケの導入が有効です。
本記事では、製造業におけるポカヨケの概要やメリット、デメリット、導入事例などについて解説します。
目次
ポカヨケとは?
ポカヨケとは、製造業やサービス業などで起きるヒューマンエラーを防止する装置のことです。規格外の製品などを次の工程に流さないことや、異品があった場合アラートが鳴る仕組みなどがポカヨケになります。
ヒューマンエラーを未然に防止することで、生産効率の向上や品質の安定、安全性の向上などを図ることができます。
ポカミスが起こる理由
行動エラー | 作業手順や指示通りに行わない、間違った方法で作業してしまうなどのミス |
---|---|
記憶エラー | 作業手順や指示を忘れてしまう、間違って覚えてしまうなどのミス |
判断エラー | 状況を正しく判断できず、間違った判断をしてしまうミス |
認知エラー | 情報の誤認や理解の誤りなどによって、間違った認識をしてしまうミス |
ルール違反 | 作業ルールやマニュアルを守らずに作業してしまうミス |
行動エラー
部品の組み付け作業で、部品の形状や位置を間違って組み付けてしまう、機械操作で、操作ボタンを間違って押してしまうなどのミスです。行動エラーは、作業者の習熟度や経験によって起こる場合があります。また、作業環境が悪い場合にも起こりやすくなります。
記憶エラー
作業手順書の確認を忘れてしまう、作業指示を間違って覚えてしまうなどのミスです。記憶エラーは、作業者の集中力や注意力によって起こる場合があります。また、作業量が多い場合や、作業が複雑な場合にも起こりやすくなります。
判断エラー
異常を正しく判断できず、そのまま作業を進めてしまう、安全性を考慮した判断ができず、危険な作業をしてしまうなどのミスです。判断エラーは、作業者の経験や知識によって起こる場合があります。また、作業が緊急の場合や、判断に時間がかかる場合にも起こりやすくなります。
認知エラー
図面の読み間違い、指示内容の誤解などのミスです。認知エラーは、作業者の集中力や注意力によって起こる場合があります。また、作業環境が悪い場合にも起こりやすくなります。
ルール違反
安全対策を怠ったまま作業をしてしまう、作業環境を整えずに作業をしてしまうなどのミスです。ルール違反は、作業者の意識やモチベーションによって起こる場合があります。
このように人が作業する業務は、注意しても起こる可能性があります。
ポカヨケを導入するメリット
ポカヨケを導入することで、以下の4つのメリットが得られます。
- ● 品質管理の向上
- ● 教育コスト削減
- ● 生産性の向上
- ● 安全性の確保
品質管理の向上
不良品の発生を防止することができます。不良品の発生を防止することで、製品の品質が向上し、顧客満足度の向上につながります。
製造業では、部品の組み付けミスや異物の混入を防止するためのポカヨケが活用されています。
教育コスト削減
作業者が入れ替わるたびに管理者が都度説明をしていると、管理者の手間になってしまいます。ポカヨケによって作業手順やマニュアルを簡素化することで、教育コストを削減することができます。
生産性の向上
作業の失敗や間違いを事前に防ぐことで作業途中に防止することで、作業効率を向上させることができます。
これにより1つの工程を改善するだけでなく、ライン全体の生産性を向上させることができます。
安全性の確保
作業者の事故の可能性を減らすことに繋がります。危険物を使用した作業などは、重大な損害をもたらす可能性があります。ポカヨケの導入によって事故は未然に防ぐことができ結果として職場の安全性の確保に繋がります。
ポカヨケを導入するデメリット
ポカヨケを導入するデメリットは、以下があげられます。
- ● 現場との連携
- ● ポカヨケへの理解
現場の作業者や管理者は、ポカヨケの重要性や効果を十分に理解していない場合があり、今までのプロセスから新しいことに変える抵抗感をおぼえる人もいます。
ポカヨケへの連携や理解を深めるには、現場の作業者や管理者と十分に連携し、ポカヨケの仕組みや装置を理解してもらう必要があります。またポカヨケの導入後も、作業者への教育を継続することで連携や理解を深めることができるでしょう。
ポカヨケを最大限活用する方法5つ
ポカヨケを導入しても、効果を十分に発揮できていないケースは少なくありません。ポカヨケを最大限活用するためには、以下の5つのポイントを押さえることが重要です。
- ● ポカミスの状況を確認する
- ● 業務の属人性を排除する
- ● 適切な工具を使用する
- ● 製造現場に必要な5S活動を浸透させる
- ● 危険予知訓練を実施する
ポカミスの状況を確認する
ポカミスの状況を確認することで、適切なポカヨケの仕組みや装置を導入することができます。
例えば、製造業で部品の組み付けミスが頻発している場合、部品の形状や位置をわかりやすく表示するポカヨケを導入することで、ミスを防止することができます。
業務の属人性を排除する
業務の属人性を排除することで、作業者の経験やスキルに左右されずに、一定の品質を維持することができます。
業務の属人性を排除するためには、作業手順の明確化、自動化にすることでポカミスを防止することができます。
適切な工具を使用する
適切な工具を使用することで、作業者の負担を軽減し、ミスを防止することができます。例えば、ネジの締め付け作業で、適切なトルクレンチを使用することで、ネジの緩みや締めすぎによるポカミスを防止することができます。
製造現場に必要な5S活動を浸透させる
5S活動とは、整理・整頓・清掃・清潔・しつけの5つの活動を組み合わせた活動です。5S活動を浸透させることで、作業者の集中力を高めミスを防止することができます。
危険予知訓練を実施する
危険予知訓練とは、作業における危険を予知し、対策を講じる訓練です。危険予知訓練を実施することで、作業中の事故を防止することができます。危険予知訓練を実施するために、作業の危険を洗い出し危険を予知するための方法を学びましょう。
ポカヨケ導入事例
ポカヨケを導入する際には、治具を活用するケースが多くあります。治具とは、作業を効率化や正確化するために使用する道具や装置のことです。治具を活用することで、作業者が作業手順を間違えるなどのミスを防止することができます。
ひとつのポカヨケ導入事例として、部品の組み付けミスを防止するために治具を導入しました。従来は、作業者が部品の形状や位置を確認しながら組み付けを行っていましたが、部品の形状や位置が複雑なためミスが発生していました。
そこで、部品の形状や位置を合わせるための治具を導入しました。治具を活用することで、部品の組み付けミスが大幅に減少することができました。
ポカヨケとは生産・品質管理・安全性を向上させる取り組み
製造業においては、部品の組み付けや機械操作など、さまざまな作業において、ヒューマンエラーによる不良品の発生や事故の発生が課題となっているため、ポカヨケは、製造業において欠かせない取り組みです。
RICOH SC-20は、組立工程での作業ミスを検査する作業検査カメラで、作業中のリアルタイムでの品質チェックが可能です。類似部品や欠品、作業順序などの組立状況を自動でチェックでき、作業ミスを防止することができます。