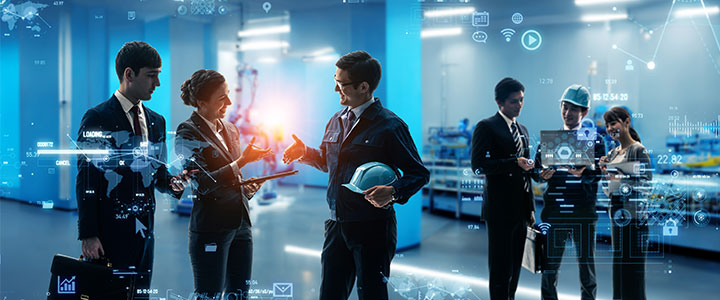
製造業DXにはさまざまなメリットがあり、すでに待ったなしで各社での取り組みが始まっています。しかし具体的にどのような取り組みが可能で、どんな効果が現れているのかが分からないため二の足を踏んでおられる企業様もおられるのではないでしょうか。本コラムでは、実際に当社リコーで取り組んだ製造業DXの成功事例をご紹介。さらに、製造業DXの取り組みを始める際のポイントについても解説します。製造業DXを推進する際の具体的なイメージをお持ちになりたい方はぜひ参考にしてください。
目次
製造業におけるDXとは
製造業におけるDXとは、最新のデジタル技術を活用してさまざまな製造工程における情報を一元化することで、生産性や安全性、品質などを向上させながら、同時にコストダウンも図る取り組みのことを言います。製造業特有の課題を解決することを目的として数多くの具体的な取り組みが始まっており、すでに実績も現れています。
具体的な例としては、RFIDを活用した入出庫管理や構内物流、工程管理があります。仕入元からの現品票をRFID化して入荷ゲートで読み込ませることで受入・検収作業を効率化させたり、指示書をRFID化して工程内のアンテナで読み込ませることで、着手・完了の状況を自動的に見える化することができます。
また、無人搬送車(AGV)を導入することで、構内物流の無人化・省人化を実現する例もあります。さらに、画像認識技術を用いて間違いやすい部品や組立状態を作業前にチェックすることで作業ミスを防いだり、部品のシリアルナンバーを認識して作業時間などの実績を記録し、作業分析やトレーサビリティーなどに活用することもできます。
製造業のDXのメリットと課題
続いて、製造業DXのメリットにはどのようなものがあるかを考えてみましょう。
生産性向上
製造業DXではさまざまな製造プロセスをデジタル化/自動化することで、同じ工程でも従来よりも迅速に処理できるようになります。さらに、人が介在することで発生するヒューマンエラーを抑止できるので品質や歩留まりなどが改善。これらにより生産性が向上します。
人手不足の解消
人口減少および少子高齢化の影響で今後も生産人口の減少が見込まれています。そのような状況下では、今後ますます労働力確保が大きな課題となってくるでしょう。DXによってより少ない労働力で従来の製造工程をまかなえるようになり、人手不足解消につながります。
人件費の削減/人的リソース再配分
既存の生産ラインをDXによって省人化・無人化していくことで、その分の人件費を削減できます。余剰になった人員をより高度な業務や重要な業務に再配分することで、製造工程の最適化や市場変化に対応する適応力を高めることができるようになります。
属人化の防止/解消
作業や検査工程をDXによって見える化することで、個々人に依存していた技術や技量を誰でも均一の品質でこなすことができるようになります。また、熟練工が有する高度な技術の継承も行いやすくなり、技術継承の問題解決にもつながっていきます。
一方、製造業DXを推進するうえで課題となるのが、専門の人材不足と新たな投資が必要になることです。DXはさまざまな分野で着目されており、それを担う人材はIT関連に加えて各分野における業務知識も必要になります。そのような人材は多くの企業から求められることになるため、供給が追いついていません。また、DXにはほとんど場合新たなシステム投資が必要になりますが、そのための投資予算確保が課題になる場合があります。
製造業のDX取り組み事例① - 無人搬送車(AGV)を活用して構内物流を効率化
製造業DXの取り組み事例として、当社が開発した「リコー 無人搬送車 M2」(以下、M2)の活用事例をご紹介します。
無人搬送機(以下、AGV)は、あらかじめ設定したルートに従って自動的に目的地まで移動する搬送型ロボットです。従来、床に貼った磁気テープで誘導するタイプが一般的でしたが、M2は当社独自の画像認識技術を生かして開発した光学式のAGVです。AGVを導入することで、ハンドリフトなどで行っていた運搬作業が不要になり、作業効率が向上。作業ムラも抑えることができます。人手の場合は、搬送可能な重さや移動距離に相当の制限がありますが、AGVではそれらの制限を大幅に拡張。搬送作業に付きものの荷崩れによる破損や衝突事故による怪我の発生も防止できます。
M2はPC上から複数台のAGVの運行管理ができ、各AGVの行き先や現在地、状態なども監視することができます。また、行き先指定などを遠隔から操作することも可能です。さらに、エレベーター制御盤と連携すれば、AGVをエレベーターに自動乗降させることもできるようになります。(※一部連携できないエレベーターもあり)
当社グループの厚木工場では実際に23台のM2を導入。生産ライン無人化や省人化を実現しています。
>構内物流の省人化 ~無人搬送車(AGV)を活用して構内物流を効率化~
製造業のDX取り組み事例② - リアルタイム監視で品質管理の負担を改善
製造現場におけるさまざまなデータを、リアルタイムかつ一元的に監視することで品質管理工数削減を実現し、ひいては製品の品質向上につながるようなDXの取り組み事例もあります。
当社の複写機パーツ部品生産においては湿温度の影響を受けやすいパーツがあり、その管理が重要になります。従来は作業員が月1~2回の頻度で温度計から抜き出したデータを加工して使用していました。その後外部に生産を移管しましたが、その際には生産環境がリアルタイムで把握できないという課題がありました。
そこで、当社の「RICOH EH 環境センサー D201」(以下、D201)を生産工場各所に設置。Wi-Fiを通じて温度データをワイヤレスかつリアルタイムで収集できる仕組みを構築しました。D201は、温度、湿度、照度、気圧、内蔵リチウムイオン電池電圧の測定が可能が超小型センサーです。設置時の配線工事や電池交換が不要で、Windowsパソコンやスマートフォンと連携してデータのモニタリングができます。
同センサーを使ってリアルタイム監視できる環境を構築したことで、作業員が逐一行っていた温度データの抜き出しや電池交換作業や不要になり、生産管理に関わる間接工数が削減。さらに、空調機故障などによる温度異常が発生してもリアルタイムで把握できるため、品質低下や生産ロス発生のリスクを大幅に抑制することができています。今回構築したリアルタイム監視の仕組みは、当社内で実証した後に生産委託先に展開しました。
製造業のDX取り組み事例③ - 作業支援カメラシステムによる画像認識で作業ミスを防止
カメラによる画像認識技術により、製造現場において作業ミスを防止した取り組み事例をご紹介します。
作業支援カメラシステムであるRICOH SC-10Aは、事前に登録した正しい作業結果の画像と現在の撮影画像を比較するパターンマッチングにより、類似部品や欠品、作業順序などの組み立て状況を作業途中に自動でチェックする機能があります。そのため、間違いやすい部品や組立状態を作業前に画像認識でチェックすることが可能で、作業の上でも画像認識で許可されないと次に進めないため、作業ミスを抑止することができます。
また、部品のシリアルナンバーや作業時間などの実績や作業結果の画像を記録できるため、作業分析やトレーサビリティーにも活用することも可能です。
作業支援カメラシステムは製造現場における、配膳・ピッキング工程、組立て工程、検査工程、出荷工程の各工程において、作業ミス防止の取り組みの一つとして活用されています。
例えば、あるメーカーでは、不良品が発生しないよう社内で厳しい規定を設けており、比較的習熟が短い従業員が作業した際の作業ミスを無くし品質を維持していくことが課題でした。そこで、作業支援カメラシステムを導入することで、作業の順番を間違えた時点でアラートがなるような仕組みを実現し、作業ミスを撲滅することに成功しています。
このように間違えることが無い環境づくりを行うことで、組み立て工程において部品の組付けミスや、チェック工程では目視チェック漏れを防止することが可能です。
製造業のDX取り組み事例④ - AI活用による製造工程での工程監視工数低減
生産プロセスデータをAIを用いて解析、活用することで工程監視工数の低減、異常の早期発見を実現した改善事例をご紹介します。
製造現場では安定した品質の製造を続けるため生産ラインを監視しています。設備の閾値による正常・異常の判断だけなら自動化とアラートで対応可能ですが、実際の現場には経験者の長年のノウハウによる異常検知が必要とされていました。また工程が長くなればなるほど、属人性のある生産データ監視は作業者への負担が大きくなります。さらに、製造条件や設備状態など稼働情報の確認業務が多く、無駄な工数も多くかかっており、、管理の簡略化や監視業務が課題となっていました。
そこで、過去の生産データをAIが学習し、自動的に正常範囲を設定。正常範囲から逸脱した際に、通常と異なる状態(=異常)と判定するシステムを構築しました。その結果、生産データ監視作業は95%低減され、監視業務の負担は大きく削減された結果となりました。また、AIによるアラートがあった場合のみ、作業者が現地確認をする体制を構築したことで、渋滞よりも大幅に早く設備故障を検知できるようになりました。
>製造工程での工程監視工数低減(生産データ確認作業の自動化と異常の自動検出)
先ずは自社のDXの度合いを知ることが重要
上記のとおり、製造業DXには生産性向上や人手不足の解消など多くのメリットがあります。しかし同時に、DXを推進するための専門人材が不足しているという課題がありました。そして、具体的にDXを進める際には、まず現状を把握した上でDXによって何を達成すべきかの目的(ゴール)を明確にすることが重要です。リコーでは製造現場のデジタル化度合いを把握するための「デジタル化診断」を無料で提供しています。「デジタル化」「調達」「製造」「検査」「出荷」「5S」の6分野におけるデジタル化への取り組み状況を5段階評価でスコア化。対象の製造現場のデジタル化適合度を客観的に把握することができます。製造業DXの最初の一歩としてまずはここから始めてみてはいかがでしょうか。